Pharmaceutical Manufacturing with Robotics in Hazardous Environments
As the Operations Director of a pharmaceutical manufacturing facility, you understand the challenges and complexities involved in ensuring the efficiency, safety, and compliance of your operations. In today's rapidly evolving landscape, the integration of advanced robotics into hazardous environment operations presents a promising solution to enhance productivity while mitigating risks.
In this blog, we look into the transformative potential of integrating robotics, specifically in hazardous environments, and how this integration, coupled with sophisticated software systems like PlanetTogether and leading ERP, SCM, and MES platforms such as SAP, Oracle, Microsoft, Kinaxis, and Aveva, can revolutionize pharmaceutical manufacturing.
Robotics in Hazardous Environments
Pharmaceutical manufacturing often involves working with hazardous materials and processes, including potent compounds, chemical reactions, and stringent containment requirements. Traditional manual operations in such environments pose significant risks to worker safety, product quality, and regulatory compliance. Additionally, the industry faces increasing pressure to improve efficiency, reduce costs, and accelerate time-to-market while maintaining the highest standards of safety and quality. This confluence of factors underscores the critical need for innovative solutions such as robotics to address these challenges effectively.
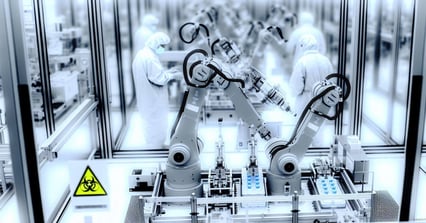
Enter Advanced Robotics
Advanced robotics technologies have witnessed remarkable advancements in recent years, making them increasingly viable for deployment in hazardous environments. These robots are equipped with sophisticated sensors, precision actuators, and intelligent control systems, enabling them to perform intricate tasks with precision, speed, and reliability. In pharmaceutical manufacturing, robots can be utilized for a wide range of applications, including material handling, dispensing, mixing, compounding, packaging, and quality control.
Benefits of Integrating Robotics
The integration of robotics into hazardous environment operations offers a myriad of benefits that can significantly enhance manufacturing efficiency, safety, and compliance:
Enhanced Safety: By automating hazardous tasks, robots minimize direct human exposure to potentially harmful substances, reducing the risk of accidents, injuries, and occupational illnesses. This not only safeguards the health and well-being of workers but also ensures compliance with stringent safety regulations.
Improved Productivity: Robots can perform repetitive tasks tirelessly and consistently, thereby increasing throughput and operational efficiency. By streamlining processes and reducing cycle times, pharmaceutical manufacturers can optimize resource utilization and meet production demands more effectively.
Precision and Accuracy: The inherent precision of robotic systems ensures consistent quality and uniformity in manufacturing processes. Whether it's dispensing precise quantities of ingredients or conducting intricate assembly tasks, robots deliver unparalleled accuracy, minimizing variations and deviations in product quality.
Flexibility and Adaptability: Modern robotics platforms are designed to be highly flexible and adaptable, allowing them to accommodate diverse production requirements and changing operational needs. With programmable capabilities and modular configurations, robots can swiftly adjust to new tasks, formulations, or product variations, enabling agile manufacturing practices.
Data-driven Insights: Robotics integration facilitates real-time data capture and analysis, providing valuable insights into production performance, process efficiency, and quality metrics. By leveraging this data, operations directors can identify optimization opportunities, implement predictive maintenance strategies, and drive continuous improvement initiatives.
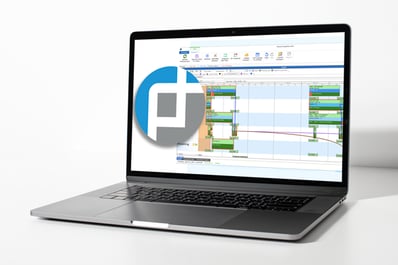
Integration with PlanetTogether and ERP, SCM, MES Systems
The seamless integration of robotics with advanced planning and enterprise resource management systems is pivotal to unlocking their full potential in pharmaceutical manufacturing. Platforms like PlanetTogether offer comprehensive production planning and scheduling functionalities, enabling operations directors to optimize resource allocation, minimize bottlenecks, and maximize throughput.
When integrated with leading ERP, SCM, and MES systems such as SAP, Oracle, Microsoft, Kinaxis, and Aveva, these solutions create a unified ecosystem that synchronizes production activities, inventory management, and supply chain operations in real time.
Key Integration Benefits Include
End-to-End Visibility: Integration between robotics, PlanetTogether, and ERP, SCM, MES systems provides operations directors with holistic visibility into manufacturing processes, from raw material procurement to finished product distribution. This comprehensive oversight enables proactive decision-making, risk mitigation, and performance monitoring across the entire value chain.
Seamless Data Exchange: By establishing seamless data exchange protocols, integration enables bidirectional communication between robotics systems and enterprise software platforms. This interoperability facilitates synchronized planning, execution, and reporting, ensuring data integrity and consistency throughout the production lifecycle.
Dynamic Resource Optimization: Integration empowers operations directors to dynamically optimize resource allocation based on real-time demand signals, production constraints, and inventory levels. By aligning production schedules with market demand and resource availability, manufacturers can minimize waste, reduce lead times, and enhance customer responsiveness.
Compliance and Traceability: Integrated systems enable automated data capture and documentation, ensuring compliance with regulatory requirements and quality standards. By maintaining accurate records of production processes, materials usage, and batch histories, manufacturers can demonstrate product traceability and adherence to Good Manufacturing Practices (GMP).
Continuous Improvement: Integration fosters a culture of continuous improvement by facilitating data-driven analytics, performance monitoring, and feedback loops. Operations directors can leverage actionable insights to identify inefficiencies, optimize workflows, and drive operational excellence initiatives across the organization.
The integration of advanced robotics into hazardous environment operations represents a transformative opportunity for pharmaceutical manufacturers to enhance productivity, safety, and compliance. By leveraging sophisticated software systems like PlanetTogether and leading ERP, SCM, and MES platforms, operations directors can orchestrate seamless collaboration between robotics, production planning, and enterprise management functions.
This integrated approach enables manufacturers to unlock new levels of efficiency, agility, and innovation, positioning them for sustained success in an increasingly competitive landscape. As we continue to embrace the era of Industry 4.0, harnessing the power of robotics integration will be paramount in driving the future of pharmaceutical manufacturing forward.
Are you ready to take your manufacturing operations to the next level? Contact us today to learn more about how PlanetTogether can help you achieve your goals and drive success in your industry.