Collaborative Planning for Synchronized Multi-Plant Scheduling
Efficient planning and scheduling are essential for food and beverage manufacturing facilities. Purchasing Managers play a pivotal role in ensuring that raw materials are procured and utilized optimally to meet production demands while minimizing costs.
To achieve this, integrating advanced planning and scheduling solutions like PlanetTogether with enterprise resource planning (ERP), supply chain management (SCM), and manufacturing execution systems (MES) is becoming increasingly essential.
In this blog, we will explore the concept of collaborative planning for synchronized multi-plant scheduling, focusing on the integration between PlanetTogether and leading ERP, SCM, and MES systems such as SAP, Oracle, Microsoft, Kinaxis, and Aveva.
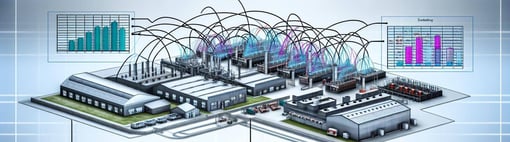
Multi-Plant Scheduling
Managing scheduling across multiple plants is a complex endeavor. Each plant may have unique production capabilities, capacity constraints, and lead times. Additionally, fluctuations in demand, supply chain disruptions, and variations in raw material availability add further complexity to the scheduling process. Purchasing Managers are tasked with procuring raw materials efficiently and ensuring that production schedules are synchronized across all plants to meet customer demands while keeping costs in check.
Traditionally, scheduling in multi-plant environments has been a manual and time-consuming process. It often involves spreadsheets, emails, and phone calls, leading to delays, errors, and missed opportunities for optimization. To address these challenges, organizations are turning to advanced planning and scheduling solutions.

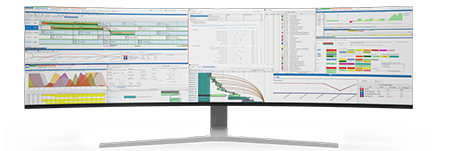
The Role of Advanced Planning and Scheduling (APS) Software
Advanced Planning and Scheduling (APS) software, such as PlanetTogether, are designed to streamline the scheduling process and help organizations make informed decisions in real-time. These systems consider various factors like production capacity, resource availability, lead times, and demand variability to create optimal schedules. However, the true power of APS software is realized when they are seamlessly integrated with ERP, SCM, and MES systems.
Integration Benefits
Real-Time Data Sharing
Integration allows for the real-time exchange of data between PlanetTogether and ERP systems like SAP and Oracle. This means that when there is an update in production schedules, material requirements, or inventory levels, this information is instantly reflected across all systems. Purchasing Managers can make informed decisions based on the latest data, reducing the risk of errors caused by outdated information.
Improved Visibility
With integration, stakeholders have access to a holistic view of the entire supply chain. They can monitor production progress, track inventory levels, and identify potential bottlenecks or delays. This visibility enables proactive decision-making, such as expediting critical orders or adjusting production plans to meet changing demand.
Enhanced Collaboration
Collaboration is at the heart of collaborative planning. Integration between PlanetTogether and systems like Microsoft Dynamics fosters collaboration by enabling teams from different departments to work together seamlessly. For example, the Purchasing team can align procurement with production schedules, ensuring that raw materials are available when needed.
Optimal Resource Utilization
APS software like Kinaxis RapidResponse and Aveva MES help optimize resource utilization by considering production constraints and capacity limitations. Integration ensures that these constraints are taken into account during scheduling, resulting in efficient use of equipment and personnel.
Faster Response to Changes
In today's fast-paced business environment, responsiveness is crucial. Integration between PlanetTogether and ERP, SCM, and MES systems enables organizations to quickly adapt to changes in demand or supply. Whether it's a sudden increase in orders or a supply chain disruption, the integrated system can automatically adjust schedules to minimize disruptions.
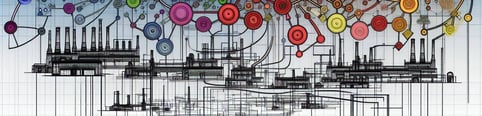
Choosing the Right Integration Approach
Integrating PlanetTogether with ERP, SCM, and MES systems is a strategic decision that requires careful planning. Organizations should consider factors such as compatibility, scalability, and ease of maintenance when choosing an integration approach. Here are some common integration methods:
API Integration
Application Programming Interface (API) integration allows for seamless data exchange between systems. It offers flexibility and real-time synchronization, making it suitable for dynamic scheduling environments. Organizations can work with software developers or vendors to implement API integration.
Middleware Solutions
Middleware solutions act as intermediaries between systems, facilitating data transfer and translation. This approach can be beneficial when dealing with legacy systems that may not have native API support. Middleware solutions like MuleSoft or Dell Boomi can bridge the gap between PlanetTogether and ERP, SCM, and MES systems.
Custom Integration
For organizations with unique requirements, custom integration may be the best option. This approach involves developing custom scripts or connectors to enable data exchange. While it offers maximum flexibility, it can also be resource-intensive and require ongoing maintenance.
Collaborative planning for synchronized multi-plant scheduling is essential for modern food and beverage manufacturing facilities. Purchasing Managers can play a crucial role in this process by ensuring the seamless integration of advanced planning and scheduling solutions like PlanetTogether with ERP, SCM, and MES systems.
By embracing integration, organizations can benefit from real-time data sharing, improved visibility, enhanced collaboration, optimal resource utilization, and faster responsiveness to changes. Whether it's SAP, Oracle, Microsoft, Kinaxis, Aveva, or other systems, the key is to choose the right integration approach that aligns with your organization's goals and requirements.
In an era where agility and efficiency are essential, collaborative planning powered by integrated systems is the path forward for food and beverage manufacturers seeking to stay competitive and meet customer demands in a synchronized and cost-effective manner.