Cost Optimization in Production Scheduling
Navigating through the complexities of production scheduling while ensuring cost efficiency and meeting delivery deadlines is a significant challenge in packaging manufacturing. One powerful solution lies in the integration of advanced scheduling software like PlanetTogether with Enterprise Resource Planning (ERP) systems such as SAP, Oracle, Microsoft Dynamics, Kinaxis, Aveva, and other SCM and MES systems.
This blog explores how such integration can transform cost optimization in production scheduling.
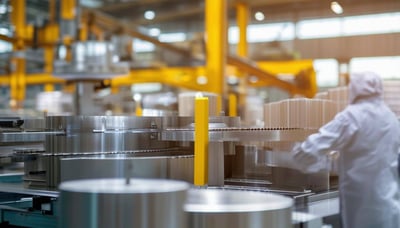
The Dynamics of Packaging Manufacturing
Packaging manufacturing is inherently complex due to its dynamic demand patterns, variety of packaging materials, and the urgent need for customization and innovation. Manufacturers often struggle with maintaining inventory levels, managing equipment downtime, and ensuring a responsive supply chain.
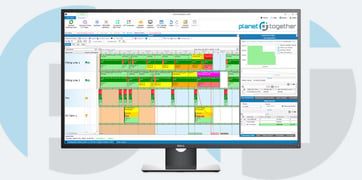
The Role of Advanced Planning and Scheduling (APS) Systems
Advanced Planning and Scheduling (APS) systems like PlanetTogether are designed to enhance manufacturing operations through better schedule accuracy, reduced inventory costs, and improved machine utilization. APS systems achieve this by using complex algorithms to predict and model scheduling scenarios.

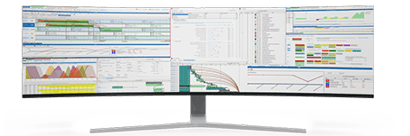
Integration of PlanetTogether with ERP Systems
SAP Integration: Integrating PlanetTogether with SAP can provide a real-time view of inventory, orders, and production capacity. SAP's powerful ERP capabilities, combined with PlanetTogether’s scheduling algorithms, allow for dynamic adjustment of production schedules based on real-time demand and supply conditions.
Oracle Integration: Oracle's ERP solutions offer robust data handling capabilities that can manage large volumes of data generated in packaging manufacturing. By integrating with PlanetTogether, manufacturers can leverage Oracle’s analytical tools to forecast demand more accurately and align production schedules accordingly.
Microsoft Dynamics Integration: Known for its user-friendly interface, integrating Microsoft Dynamics with PlanetTogether allows for smoother communication across departments. This integration helps in synchronizing production scheduling with sales forecasts and customer relationship management.
Kinaxis Integration: Kinaxis provides specialized supply chain management solutions that focus on rapid decision-making capabilities. When integrated with PlanetTogether, the combined solution can drastically reduce response times to supply chain disruptions, thereby minimizing production delays and costs.
Aveva Integration: Aveva’s MES solutions focus on operational efficiency. Integrating these with PlanetTogether helps packaging manufacturers not only in scheduling but also in real-time monitoring of the shop floor activities, thus enabling immediate adjustments to the production processes to save costs and time.
Benefits of Integration
Enhanced Visibility: Integration provides a unified view of all operations, helping Supply Chain Managers make informed decisions quickly.
Improved Resource Utilization: Effective scheduling ensures optimal use of machinery and labor, reducing idle times and overtime costs.
Increased Flexibility: Being able to respond swiftly to changes in demand or production issues is crucial. Integrated systems provide the agility needed in today’s market.
Inventory Reduction: By aligning production schedules with actual demand, companies can keep inventory levels low, reducing holding costs.
Waste Minimization: Better scheduling leads to reduced waste as production runs are planned to maximize material utilization.
For Supply Chain Managers in the packaging manufacturing sector, integrating advanced planning systems like PlanetTogether with ERP solutions such as SAP, Oracle, or Microsoft Dynamics offers a strategic advantage. It not only enhances operational efficiencies but also drives significant cost savings through optimized production scheduling.
As the industry evolves, the integration of these systems will likely become a necessity rather than an option, paving the way for smarter, more cost-effective manufacturing practices. Are you ready to take your manufacturing operations to the next level? Contact us today to learn more about how PlanetTogether can help you achieve your goals and drive success in your industry.