Crisis Management Plans
The unexpected is often an unavoidable reality in industrial manufacturing. From supply chain disruptions to equipment failures, crises can strike at any moment, posing significant threats to operations, productivity, and ultimately, profitability. As an Operations Director, your role is pivotal in ensuring your facility is equipped to effectively respond to and recover from such challenges.
In this blog, we'll look into the importance of crisis management plans and explore how integrating tools like PlanetTogether with leading ERP, SCM, and MES systems can bolster your facility's resilience in the face of adversity.
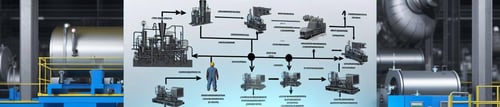
Understanding Crisis Management Plans
Crisis management plans are comprehensive strategies developed to anticipate, prevent, respond to, and recover from crises effectively. While it's impossible to predict every potential threat, having a well-defined plan in place enables organizations to mitigate risks, minimize disruptions, and maintain continuity during turbulent times.
The Need for Integration
In today's interconnected digital ecosystem, industrial manufacturing facilities rely on a myriad of software systems to streamline operations, manage resources, and optimize processes. Enterprise Resource Planning (ERP), Supply Chain Management (SCM), and Manufacturing Execution Systems (MES) are among the core platforms utilized to drive efficiency and orchestrate workflows.

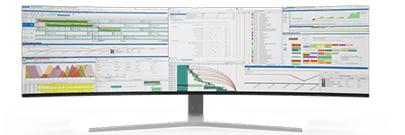
However, without seamless integration between these systems, critical data silos can emerge, hindering visibility, collaboration, and responsiveness—particularly during crises. This is where integration solutions like those between PlanetTogether and industry-leading platforms such as SAP, Oracle, Microsoft, Kinaxis, and Aveva come into play.
Benefits of Integration
Real-time Data Synchronization: Integration enables the automatic exchange of data between disparate systems, ensuring that stakeholders have access to accurate, up-to-date information across the board. This real-time visibility is crucial for making informed decisions swiftly during crisis situations.
Improved Forecasting and Planning: By integrating advanced planning and scheduling tools like PlanetTogether with ERP and SCM systems, manufacturers can enhance their forecasting accuracy and optimize production schedules based on changing demand, supply constraints, and resource availability.
Enhanced Communication and Collaboration: Integrated systems facilitate seamless communication and collaboration among cross-functional teams, enabling rapid response and coordinated efforts during crises. From supply chain disruptions to equipment breakdowns, stakeholders can quickly align on priorities and execute contingency plans effectively.
Agile Adaptation: Crises often necessitate rapid adaptation to evolving circumstances. Integration empowers organizations to quickly adjust production schedules, allocate resources efficiently, and pivot strategies in real-time, enabling them to weather storms and emerge stronger on the other side.
Streamlined Compliance and Reporting: Integration simplifies compliance management by ensuring that regulatory requirements are seamlessly embedded into workflows and processes. Moreover, consolidated data from integrated systems enables organizations to generate comprehensive reports and insights for post-crisis analysis and continuous improvement.
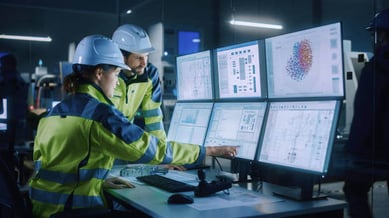
Key Components of an Effective Crisis Management Plan
While the specifics may vary depending on the nature of your operations and industry, an effective crisis management plan typically includes the following components:
Risk Assessment and Identification: Conduct a thorough risk assessment to identify potential threats and vulnerabilities within your operations, supply chain, and external environment.
Preventive Measures: Implement proactive measures to mitigate identified risks, such as redundancies in critical systems, supplier diversification, and disaster recovery protocols.
Response Framework: Develop a clear framework outlining roles, responsibilities, and communication channels for responding to crises. Establish escalation procedures and decision-making criteria to ensure swift and decisive action when necessary.
Resource Allocation: Identify key resources—including personnel, equipment, and materials—and establish protocols for their allocation and utilization during crises.
Training and Drills: Regularly conduct training sessions and crisis simulations to familiarize personnel with emergency procedures, test the effectiveness of the crisis management plan, and identify areas for improvement.
Continuous Improvement: Periodically review and update your crisis management plan to reflect changes in the operating environment, emerging risks, and lessons learned from past incidents.
In an industry where volatility is the norm rather than the exception, having a robust crisis management plan is not just advisable—it's imperative. By integrating tools like PlanetTogether with leading ERP, SCM, and MES systems, industrial manufacturing facilities can fortify their resilience, optimize response capabilities, and emerge stronger from crises.
As an Operations Director, your leadership in championing the development, implementation, and continuous improvement of crisis management plans is instrumental in safeguarding your facility's operations, reputation, and bottom line.
Are you ready to take your manufacturing operations to the next level? Contact us today to learn more about how PlanetTogether can help you achieve your goals and drive success in your industry.