Zero-Waste Manufacturing: Sustainable Solutions
The need for sustainability has become more crucial than ever in the industrial landscape. Chemical manufacturing, in particular, stands at a crossroads, where the traditional methods of production are being reevaluated in favor of more environmentally friendly practices. One such paradigm shift is the adoption of zero-waste manufacturing principles.
In this blog, we look into the significance of zero-waste manufacturing for chemical facilities, exploring its benefits, challenges, and the role of advanced IT solutions in its successful implementation.
Zero-Waste Manufacturing
Zero-waste manufacturing is not merely a lofty ideal but a pragmatic approach towards minimizing waste generation and maximizing resource utilization throughout the production process. At its core, zero-waste manufacturing aims to eliminate waste streams by redesigning processes, optimizing material usage, and fostering a circular economy mindset. For chemical manufacturing facilities, this entails rethinking conventional practices and leveraging innovative technologies to achieve sustainable outcomes.
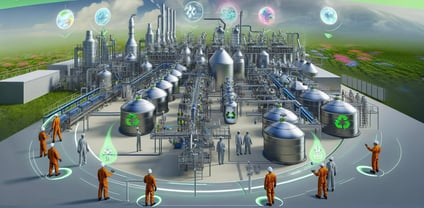
The Benefits of Zero-Waste Manufacturing in Chemical Facilities
Environmental Preservation: By reducing waste generation and minimizing environmental impact, zero-waste manufacturing contributes to the preservation of ecosystems and natural resources. This aligns with the growing societal demand for eco-friendly products and processes.
Cost Savings: Embracing zero-waste principles can lead to significant cost savings for chemical manufacturers. By streamlining processes, optimizing resource utilization, and minimizing waste disposal expenses, companies can enhance their operational efficiency and improve profitability in the long run.
Regulatory Compliance: With stringent environmental regulations governing the chemical industry, zero-waste manufacturing offers a pathway to compliance. By adopting sustainable practices and reducing emissions, companies can mitigate regulatory risks and enhance their reputation as responsible corporate citizens.
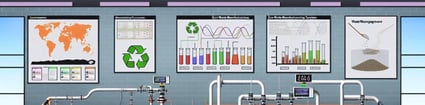
Challenges in Implementing Zero-Waste Manufacturing
Despite its numerous benefits, the transition to zero-waste manufacturing poses several challenges for chemical facilities:
Cultural Shift: Embracing a zero-waste mindset requires a cultural shift within the organization. Employees at all levels must be committed to sustainability goals and willing to embrace change.
Technological Integration: Integrating zero-waste principles into existing manufacturing processes requires advanced IT solutions capable of optimizing resource utilization and facilitating real-time monitoring and analysis.
Supply Chain Complexity: Chemical manufacturing involves intricate supply chains with multiple stakeholders. Coordinating efforts across the supply chain to minimize waste generation and maximize resource efficiency can be challenging.
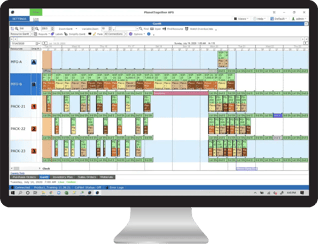
The Role of IT Solutions in Zero-Waste Manufacturing
In the digital age, advanced IT solutions play a pivotal role in driving sustainable practices within chemical manufacturing facilities. Integration between manufacturing execution systems (MES), enterprise resource planning (ERP), and supply chain management (SCM) platforms is essential for streamlining operations and maximizing resource efficiency.
One such integration is between PlanetTogether, a leading production planning and scheduling software, and ERP systems like SAP, Oracle, Microsoft Dynamics, Kinaxis, and Aveva. This integration enables seamless data exchange between production planning and enterprise resource management, facilitating real-time decision-making and optimizing resource allocation.
By leveraging advanced analytics and predictive modeling capabilities, integrated IT solutions provide valuable insights into production processes, identifying opportunities for waste reduction and efficiency improvement. Additionally, MES systems enable detailed tracking of material flows, energy consumption, and emissions, enabling chemical manufacturers to monitor their environmental footprint and identify areas for improvement.
The adoption of zero-waste manufacturing principles holds immense potential for chemical manufacturing facilities seeking to achieve sustainable resource utilization. By embracing a holistic approach that combines technological innovation, process optimization, and cultural transformation, companies can minimize waste generation, reduce environmental impact, and improve operational efficiency.
Integrated IT solutions, such as the integration is between PlanetTogether, a leading production planning and scheduling software, and ERP systems, play a crucial role in facilitating this transition by enabling real-time data exchange, advanced analytics, and collaborative decision-making across the organization.
As the industry continues to evolve, embracing zero-waste manufacturing will not only drive environmental stewardship but also unlock new opportunities for growth, innovation, and long-term sustainability. Are you ready to take your manufacturing operations to the next level? Contact us today to learn more about how PlanetTogether can help you achieve your goals and drive success in your industry.