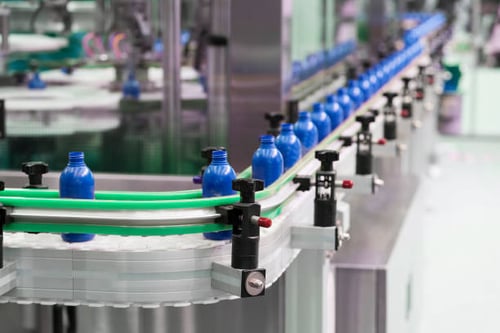
Enhancing Operational Resilience and Agility in Chemical Manufacturing with Advanced Planning Systems
For Operations Directors in the chemical manufacturing sector, ensuring consistent output amidst volatility is more than a challenge—it’s a business imperative. The combination of shifting market demands, global supply chain disruptions, labor shortages, and regulatory pressures demands a new approach to planning and execution. Operational resilience—the ability to anticipate, respond, and adapt to disruptions—must be paired with agility, enabling rapid changes to production schedules, supply inputs, or distribution priorities.
To achieve this, many leading chemical manufacturers are turning to Advanced Planning and Scheduling (APS) solutions like PlanetTogether, especially when seamlessly integrated with ERP systems such as SAP, Oracle, Microsoft Dynamics, Kinaxis, or Aveva. Together, they form a digital backbone that supports real-time responsiveness, cross-functional visibility, and robust scenario modeling.
The Case for Operational Resilience and Agility
Why Resilience Matters in Chemical Manufacturing
Chemical manufacturers operate in a high-stakes environment. From batch traceability and hazardous material handling to compliance with REACH or OSHA, even minor disruptions can have cascading effects.
Key vulnerability areas include:
Supply volatility: Unpredictable raw material availability and price spikes.
Production complexity: Blending, reactions, and quality control processes that are sensitive to variation.
Global dependencies: Multi-national plants and suppliers, each affected by regional instabilities or regulatory shifts.
Environmental factors: Extreme weather or power outages affecting energy-intensive operations.
In this context, resilience means having systems that detect, prepare, and respond to threats without sacrificing safety, quality, or profitability.
Why Agility Is the Perfect Companion
While resilience addresses the long-term capability to withstand shocks, agility is the near-term ability to pivot rapidly. For example:
Adjusting production schedules to prioritize high-demand SKUs.
Switching suppliers or transport modes due to geopolitical changes.
Implementing new formulations based on regulatory updates.
To navigate both domains, Operations Directors need unified platforms that combine forecasting, planning, production, and analytics—enabled through APS-ERP integration.
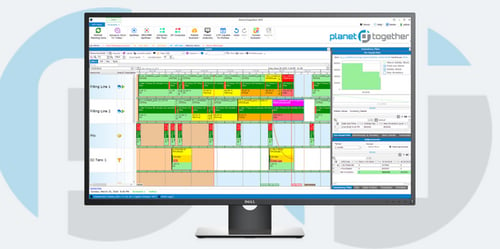
PlanetTogether APS: A Core Enabler of Resilient and Agile Operations
PlanetTogether APS is designed specifically to manage the dynamic and complex nature of manufacturing operations. It helps operations teams:
Synchronize production and procurement plans.
Balance machine and labor capacity with demand.
Model “what-if” scenarios for rapid decision-making.
Optimize for throughput, on-time delivery, and cost.
When integrated with ERP systems like SAP, Oracle, Microsoft, Kinaxis, or Aveva, the benefits expand dramatically.
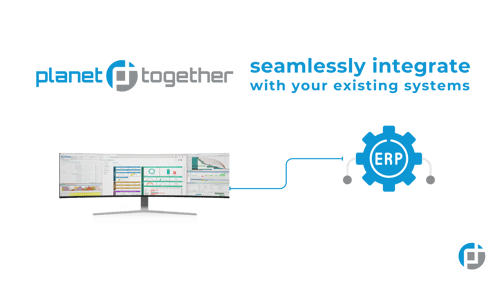
Unlocking Resilience and Agility Through Integration
Real-Time Data Synchronization
Integrated systems ensure that real-time data from the shop floor, inventory, procurement, and sales feed directly into the planning engine. This enables:
Instant alerts on inventory shortages or excesses.
Adjustments to work orders based on supplier ETAs.
Immediate reflection of quality assurance holds or batch failures.
Example: A chemical plant using PlanetTogether + SAP can automatically re-prioritize batches when a key raw material shipment is delayed, avoiding idle reactors and labor shifts.
Scenario Planning and Rapid Rescheduling
PlanetTogether’s advanced simulation capabilities allow for side-by-side comparisons of potential outcomes based on:
Supplier disruption.
Equipment breakdown.
Workforce constraints.
Integrated with Kinaxis, a supply chain orchestration platform, operations teams can analyze upstream and downstream effects of these scenarios across multiple sites, not just within one facility.
Capacity and Constraint Management
Chemical manufacturing processes often involve complex dependencies—e.g., tank availability, clean-in-place (CIP) cycles, or regulatory changeovers. Integration with Aveva’s manufacturing execution systems (MES) provides granular visibility into equipment readiness and process constraints.
By feeding this data into PlanetTogether:
Bottlenecks can be anticipated and resolved proactively.
Batch sequencing can be optimized for safety and efficiency.
Regulatory constraints can be baked into planning parameters.
Unified KPI Monitoring for Decision Support
With integration to Oracle or Microsoft Dynamics, organizations can centralize KPIs across finance, operations, and supply chain. This holistic view ensures that decisions are:
Profit-aware (margin optimization).
Service-aware (OTIF tracking).
Risk-aware (compliance and sustainability).
Result: Operations Directors can confidently choose whether to expedite a batch, defer a run, or adjust capacity without second-guessing business-wide impact.
Building a Culture of Resilient Agility
Technology alone isn't the full answer—success depends on aligning processes and people around new capabilities.
Steps to Foster Operational Agility:
Cross-functional planning meetings using live data from PlanetTogether dashboards.
Decentralized decision-making enabled by role-based access to planning tools.
Continuous training to interpret planning recommendations and override intelligently when needed.
Feedback loops between operations, procurement, and sales to refine constraint models and scheduling logic.
When PlanetTogether is tightly integrated into daily workflows, teams develop confidence in the system’s accuracy and recommendations—unlocking speed, consistency, and better outcomes.
In chemical manufacturing, resilience and agility are not optional—they’re essential. The pressures of operational continuity, environmental regulation, and customer responsiveness demand intelligent tools that work together in real-time.
By integrating PlanetTogether APS with platforms like SAP, Oracle, Microsoft Dynamics, Kinaxis, and Aveva, Operations Directors gain the digital edge required to:
Detect disruptions early.
Model decisions confidently.
Respond faster than the competition.
Maintain compliance and quality.
This isn’t just about surviving volatility—it’s about transforming uncertainty into strategic advantage.
Are you ready to take your manufacturing operations to the next level? Contact us today to learn more about how PlanetTogether can help you achieve your goals and drive success in your industry.