Machine Vision for Predictive Scheduling Adjustments
As an Operations Director, you're constantly seeking innovative solutions to enhance efficiency, optimize production schedules, and minimize defects. One cutting-edge technology that has been revolutionizing the industry is machine vision.
In this blog, we'll explore the integration of machine vision applications with predictive scheduling adjustments to address packaging defects proactively. Specifically, we'll look into how integrating PlanetTogether with leading ERP, SCM, and MES systems such as SAP, Oracle, Microsoft, Kinaxis, and Aveva can streamline operations and drive tangible improvements in quality and productivity.
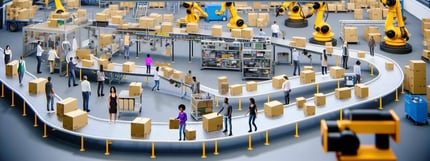
Machine Vision in Packaging Manufacturing
Machine vision refers to the use of cameras and image processing algorithms to inspect and analyze objects in real-time. In the context of packaging manufacturing, machine vision systems are deployed to detect defects, ensure product quality, and optimize production processes.
These systems are equipped with advanced sensors and software algorithms capable of identifying even the slightest imperfections in packaging materials, labels, and product contents. By capturing and analyzing images at high speeds, machine vision enables manufacturers to detect defects with precision and accuracy, thus reducing the risk of faulty products reaching consumers.
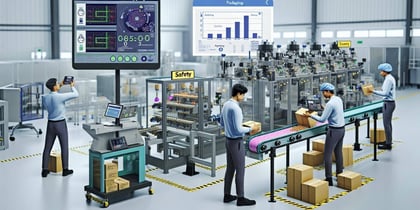
Integrating Machine Vision with Predictive Scheduling
One of the key challenges in packaging manufacturing is the need to maintain optimal production schedules while minimizing downtime and waste. Traditional approaches to scheduling often rely on reactive measures, where adjustments are made after defects or production delays have already occurred.
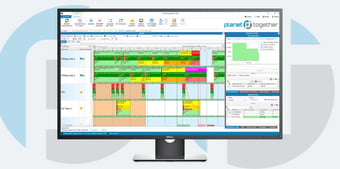
However, by integrating machine vision with predictive scheduling systems such as PlanetTogether, manufacturers can take a proactive approach to address potential issues before they escalate. Here's how it works:
Real-Time Defect Detection: Machine vision systems continuously monitor the production line, inspecting each package for defects as it moves along the conveyor belt. Any anomalies detected are immediately flagged for further analysis.
Data Integration: The data collected by the machine vision systems is seamlessly integrated with the scheduling software, providing real-time insights into production quality and performance. This integration allows for quick identification of trends and patterns that may impact scheduling decisions.
Predictive Analytics: Leveraging advanced analytics algorithms, the integrated system can forecast potential production issues based on historical data and current trends. By analyzing factors such as defect rates, machine performance, and material availability, the system can anticipate scheduling conflicts and recommend adjustments to mitigate risks.
Automated Adjustments: Based on the predictive insights generated by the system, PlanetTogether can automatically adjust production schedules in real-time to optimize efficiency and minimize the impact of defects. This may involve reallocating resources, rescheduling tasks, or prioritizing certain orders to meet quality standards and delivery deadlines.
Benefits of Integration
The integration of machine vision with predictive scheduling offers numerous benefits for packaging manufacturers:
Improved Quality Control: By detecting defects early in the production process, manufacturers can reduce the number of faulty products reaching the market, thereby enhancing customer satisfaction and brand reputation.
Increased Efficiency: Proactive scheduling adjustments help minimize downtime and optimize resource utilization, leading to higher throughput and lower production costs.
Enhanced Flexibility: With real-time insights into production performance, manufacturers can quickly adapt to changing demand patterns, market conditions, and supply chain disruptions.
Data-Driven Decision Making: By harnessing the power of data analytics, manufacturers can make more informed decisions regarding production planning, inventory management, and process optimization.
Seamless Integration: Integrating machine vision with existing ERP, SCM, and MES systems streamlines operations and eliminates data silos, ensuring a more cohesive and efficient manufacturing environment.
The integration of machine vision with predictive scheduling systems such as PlanetTogether represents a game-changer for packaging manufacturers seeking to enhance efficiency, quality, and competitiveness. By leveraging advanced technologies and data analytics, operations directors can proactively identify and address production issues, thereby driving tangible improvements in productivity and profitability.
As you continue to navigate the complexities of modern manufacturing, consider the opportunities that machine vision and predictive scheduling integration can offer to optimize your operations and stay ahead of the competition.
Are you ready to take your manufacturing operations to the next level? Contact us today to learn more about how PlanetTogether can help you achieve your goals and drive success in your industry.