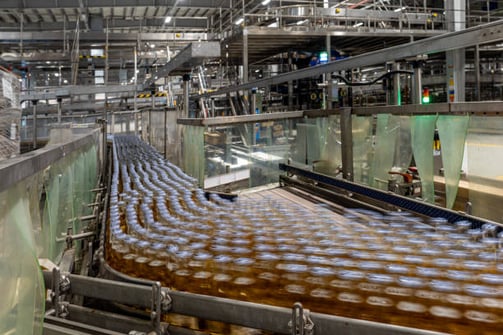
Maintaining Efficient Production in Food and Beverage Manufacturing: The Role of APS and ERP Integration
The Efficiency Imperative in F&B Manufacturing
Food and beverage manufacturing is a high-speed, high-stakes industry where efficiency is more than just a metric—it’s a mandate. With razor-thin margins, tight regulatory standards, short shelf lives, and increasing consumer expectations, Plant Managers must maintain consistent throughput while responding to variability in demand, raw material availability, and labor. In such a dynamic environment, inefficiencies anywhere in the production chain can lead to costly downtime, spoiled inventory, or lost sales.
This is where the integration of advanced planning and scheduling (APS) systems like PlanetTogether with leading ERP platforms such as SAP, Oracle, Microsoft Dynamics, Kinaxis, or Aveva can redefine the landscape of plant efficiency.
This blog explores how such integration can empower Food and Beverage Plant Managers to streamline operations, respond faster to real-world challenges, and drive continuous improvement across the production floor.
Understanding the Production Challenges in Food & Beverage
Food and beverage production presents a unique mix of constraints:
Perishable inputs and outputs require precise scheduling to prevent spoilage.
Frequent changeovers due to SKU variability reduce equipment availability.
Compliance regulations demand tight tracking of ingredients and processes.
Seasonal and promotional demand spikes strain supply chain responsiveness.
Sustainability pressures necessitate waste minimization and resource efficiency.
Meeting these demands with outdated, siloed, or manual planning methods is not only difficult—it’s increasingly untenable. For Plant Managers to maintain efficient production, they need real-time visibility, optimized resource allocation, and flexible schedules that can adapt to disruptions.
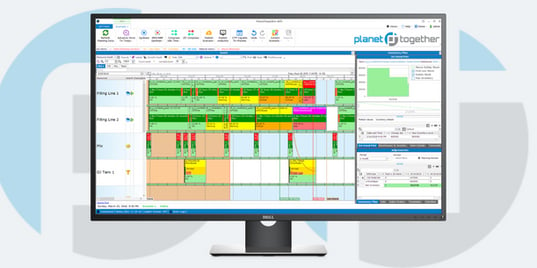
The Efficiency Benefits of APS Integration
An Advanced Planning and Scheduling (APS) system like PlanetTogether delivers powerful capabilities when fully integrated with an ERP such as SAP, Oracle, Microsoft, Kinaxis, or Aveva. The synergy of APS and ERP transforms reactive manufacturing operations into predictive, agile systems.
Key Benefits:
Real-Time Visibility: APS integration ensures real-time data flow between planning and execution layers. This helps Plant Managers make informed decisions based on the latest inventory levels, machine status, and order priorities.
Optimized Resource Utilization: APS algorithms analyze constraints across labor, equipment, materials, and shifts to generate the most efficient schedule. This minimizes idle time and reduces overproduction.
Rapid Changeover Management: By sequencing production runs intelligently, PlanetTogether reduces changeovers and clean-in-place (CIP) cycles, preserving capacity and improving throughput.
Improved On-Time Delivery: When integrated with ERP systems, APS solutions align production with actual demand, ensuring that the right products are made at the right time—without excess.
Scenario Planning: Plant Managers can run “what-if” simulations to evaluate the impact of equipment failure, supplier delays, or sudden demand changes—before they affect actual production.
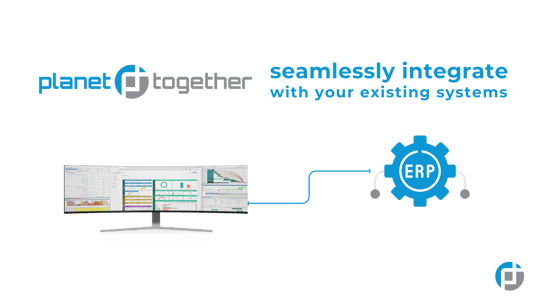
Integration in Action: How PlanetTogether Works with Leading ERPs
PlanetTogether connects seamlessly with major ERP systems, transforming raw transactional data into actionable production plans. Here’s how it works with some of the leading platforms:
SAP: Pulls production orders, inventory levels, and BOMs directly into PlanetTogether for finite scheduling. Pushes back optimized schedules to SAP for execution and performance tracking.
Oracle: Integrates with Oracle Supply Chain and Manufacturing modules to align planning and shop floor control with dynamic scheduling insights.
Microsoft Dynamics: Enables automated scheduling and resource optimization within Microsoft’s business ecosystem, with visual dashboards and alerts.
Kinaxis: Complements Kinaxis RapidResponse with detailed production scheduling, feeding predictive insights into broader supply chain orchestration.
Aveva: Enhances Aveva MES and operations management systems by providing granular production schedules, maximizing shop floor performance.
Building a Culture of Efficiency on the Plant Floor
Efficient production is not solely a result of advanced software—it also depends on plant culture and operational discipline. APS and ERP integration supports Plant Managers in developing and maintaining a culture of efficiency through:
Accountability: With real-time KPI tracking and schedule adherence metrics, team leaders can stay accountable for production targets.
Cross-Functional Coordination: Schedulers, maintenance teams, and procurement planners gain access to a single version of the truth, reducing miscommunication and downtime.
Continuous Improvement: Historical performance data captured by APS and ERP systems supports root cause analysis, lean initiatives, and overall equipment effectiveness (OEE) improvements.
Empowered Decision-Making: With integrated planning tools, Plant Managers gain the confidence to make proactive decisions rather than reacting to crisis events.
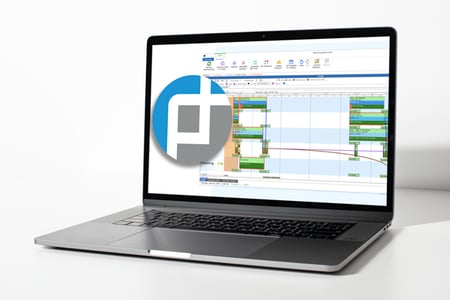
Implementation Roadmap: What Plant Managers Should Consider
To successfully integrate PlanetTogether with your ERP system, consider the following steps:
Assess Current State
Evaluate where inefficiencies, delays, or communication breakdowns occur within your current scheduling process.
Define Objectives
Set clear goals—whether it's reducing changeovers, increasing throughput, or improving on-time delivery.
Select Integration Points
Work with IT and operations to determine what data needs to flow between your ERP (SAP, Oracle, etc.) and PlanetTogether—orders, inventory, machine data, labor availability, etc.
Train Teams
Ensure that schedulers, supervisors, and planners understand the new tools and how to interpret APS-generated schedules.
Monitor & Refine
Leverage reporting tools to monitor KPIs and continuously improve based on performance feedback.
The Strategic Advantage of Integrated Efficiency
In food and beverage, maintaining efficient production isn’t optional—it’s the foundation of profitability and growth. By integrating PlanetTogether APS with ERP systems like SAP, Oracle, Microsoft, Kinaxis, or Aveva, Plant Managers gain the tools they need to orchestrate complex operations with speed and precision.
Whether it’s reducing waste, responding to demand shifts, or meeting stringent quality standards, APS-ERP integration gives you the edge to lead your plant with confidence—and keep your production floor running like clockwork.
If you're exploring ways to enhance scheduling efficiency or prepare for a broader digital transformation, consider starting with a pilot integration between PlanetTogether and your current ERP. Efficiency doesn’t just happen—it’s engineered. With the right tools and data foundation, you can lead your plant toward a more agile, responsive, and efficient future.