Bottleneck Analysis
Production schedulers bear the weighty responsibility of orchestrating the complex dance of ingredients, machines, and manpower to ensure that products reach consumers on time and within budget. One of the most crucial challenges they face is identifying and mitigating bottlenecks in the production process.
In this blog, we will look deep into the world of bottleneck analysis in manufacturing and explore how integrating advanced planning and scheduling solutions like PlanetTogether with ERP, SCM, and MES systems can revolutionize production scheduling efficiency.
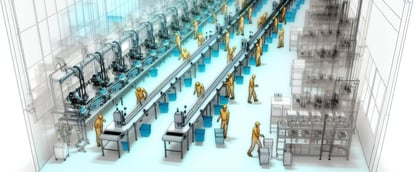
The Bottleneck Phenomenon
To begin our journey into bottleneck analysis, let's establish a clear understanding of what a bottleneck is in a manufacturing context. A bottleneck is a point in the production process where the capacity of a resource (machine, work center, or labor) is lower than the demand placed upon it. This leads to a slowdown in production and can have a cascading effect on the entire manufacturing line.
The consequences of bottlenecks in food and beverage manufacturing can be devastating. Delays, increased costs, missed deadlines, and customer dissatisfaction are just a few of the problems that can arise. Identifying and addressing bottlenecks is, therefore, essential for maintaining a competitive edge in the industry.
The Role of Production Schedulers
Production schedulers play a pivotal role in the battle against bottlenecks. Their responsibilities encompass creating and optimizing production schedules, resource allocation, inventory management, and ensuring the smooth flow of operations. To effectively tackle bottlenecks, schedulers need access to the right tools and insights.

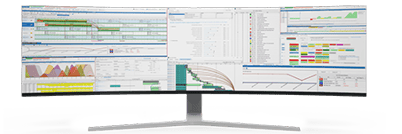
The Power of Advanced Planning and Scheduling (APS)
Advanced Planning and Scheduling (APS) solutions, like PlanetTogether, are a game-changer in the food and beverage manufacturing industry. APS systems go beyond traditional scheduling software by offering advanced algorithms and data-driven analytics to optimize production schedules. Here's how APS can help production schedulers tackle bottlenecks:
Real-time Visibility: APS systems provide real-time visibility into production processes, allowing schedulers to identify bottlenecks as they occur, rather than discovering them after the fact.
Scenario Simulation: APS software enables schedulers to run "what-if" scenarios to assess the impact of different scheduling decisions on bottlenecks and production efficiency.
Constraint-Based Scheduling: APS solutions use constraint-based scheduling algorithms to ensure that production schedules are optimized while respecting the constraints of available resources.
Demand Forecasting: By integrating demand forecasting capabilities, APS systems help schedulers anticipate spikes in demand and proactively address potential bottlenecks.
Collaboration: APS platforms facilitate collaboration among various departments within the organization, enhancing communication and problem-solving capabilities.
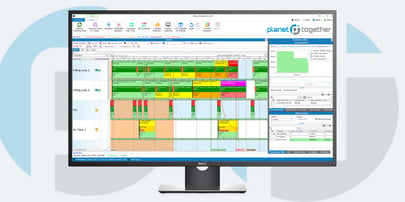
Integrating APS with ERP, SCM, and MES Systems
The true power of APS systems shines when they are seamlessly integrated with ERP (Enterprise Resource Planning), SCM (Supply Chain Management), and MES (Manufacturing Execution Systems) systems. Let's explore the benefits of such integration:
Data Integration: Integrating APS with existing systems ensures that all relevant data, including production orders, inventory levels, and resource availability, is readily available for scheduling and analysis.
Improved Decision-Making: APS systems, when combined with data from ERP, SCM, and MES, provide schedulers with a holistic view of the manufacturing process. This enables better-informed decision-making and the ability to identify bottlenecks more effectively.
Synchronization: Integration ensures that scheduling decisions made in APS are synchronized with the broader organizational strategy and objectives, leading to more efficient resource allocation.
Streamlined Communication: With data flowing seamlessly between systems, communication between departments such as production, procurement, and sales is improved, reducing the risk of bottlenecks caused by miscommunication.
Predictive Analytics: By harnessing historical data from ERP, SCM, and MES systems, APS can employ predictive analytics to anticipate bottlenecks and suggest preemptive actions.
Best Practices for Integration
Implementing APS-ERP-SCM-MES integration is a significant undertaking. Here are some best practices to consider:
Define Clear Objectives: Establish clear objectives for the integration project, such as reducing lead times, improving resource utilization, or enhancing customer service.
Cross-functional Collaboration: Involve representatives from all relevant departments in the integration process to ensure that the solution meets everyone's needs.
Data Quality: Invest in data quality initiatives to ensure that the information flowing between systems is accurate and up-to-date.
Change Management: Implement change management strategies to help employees adapt to the new integrated system and workflows.
Continuous Monitoring: Continuously monitor the performance of the integrated system and make adjustments as needed to optimize operations further.
Mastering efficiency in food and beverage manufacturing requires a keen focus on identifying and mitigating bottlenecks. Production schedulers armed with advanced planning and scheduling (APS) solutions like PlanetTogether, integrated seamlessly with ERP, SCM, and MES systems, have the tools and insights needed to tackle bottlenecks head-on.
As a production scheduler, embracing the power of integrated APS solutions could be the key to unlocking new levels of efficiency and ensuring your organization's continued success in the food and beverage industry. With the right tools and a strategic approach to integration, you can master the art of bottleneck analysis and lead your company towards a future of streamlined operations and satisfied customers.
Are you ready to take your manufacturing operations to the next level? Contact us today to learn more about how PlanetTogether can help you achieve your goals and drive success in your industry.