Production Yield: The Power of Integration in Medical Manufacturing
In medical manufacturing, where precision, efficiency, and compliance are vital, the role of the Purchasing Manager is more critical than ever. Among the myriad challenges faced, one area that demands special attention is production yield optimization. Maximizing production yield not only enhances profitability but also ensures consistent quality and timely delivery of life-saving medical devices and equipment.
In this blog, we look into the significance of production yield optimization in medical manufacturing and explore how integration between advanced planning and enterprise resource planning (ERP), supply chain management (SCM), and manufacturing execution systems (MES) can revolutionize operations. Specifically, we'll examine the synergy between PlanetTogether and leading ERP systems like SAP, Oracle, Microsoft, Kinaxis, Aveva, and others in achieving this goal.
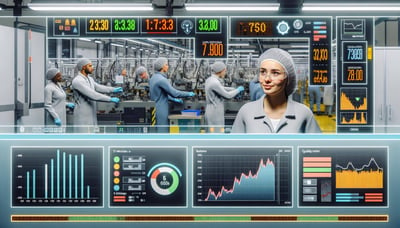
Production Yield Optimization
Production yield refers to the proportion of usable output obtained from raw materials or components in manufacturing processes. For medical manufacturers, optimizing production yield is not merely a matter of reducing waste; it's about maximizing efficiency while maintaining stringent quality standards and regulatory compliance.
Several factors influence production yield, including equipment reliability, process variability, raw material quality, and operator skill. Identifying and addressing inefficiencies at each stage of the production cycle is crucial for enhancing yield and minimizing costs.
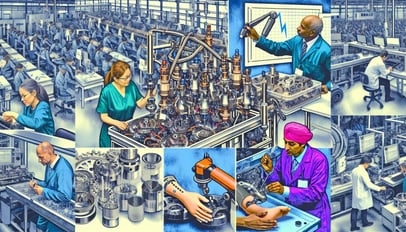
Challenges in Medical Manufacturing
Medical manufacturing presents unique challenges compared to other industries. Strict regulatory requirements, such as those outlined by the Food and Drug Administration (FDA) in the United States and corresponding agencies worldwide, demand adherence to rigorous standards throughout the production process.
Moreover, the diversity and complexity of medical devices, ranging from implants to diagnostic equipment, necessitate flexible and scalable manufacturing operations. Balancing the need for customization with mass production efficiency is a delicate task that requires careful planning and execution.
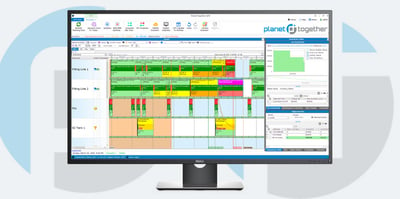
Integration: The Key to Optimization
To overcome these challenges and achieve optimal production yield, medical manufacturers must leverage advanced technologies and integrated systems. Integration between production planning tools like PlanetTogether and ERP, SCM, and MES platforms offers a holistic solution for streamlining operations, enhancing visibility, and driving continuous improvement.
Let's look into the benefits of integrating PlanetTogether with leading ERP systems:
Seamless Data Exchange: Integration facilitates seamless data exchange between PlanetTogether's advanced production scheduling and planning capabilities and the core functions of ERP systems. This enables real-time visibility into inventory levels, demand forecasts, and production schedules, empowering Purchasing Managers to make informed decisions and optimize resource allocation.
Improved Demand Forecasting: By integrating PlanetTogether with ERP systems like SAP, Oracle, or Microsoft Dynamics, medical manufacturers can enhance demand forecasting accuracy. This is essential for aligning production schedules with fluctuating customer demand, minimizing stockouts, and reducing excess inventory.
Enhanced Resource Utilization: Integrated systems enable Purchasing Managers to optimize resource utilization across the supply chain. By synchronizing production schedules with procurement processes, manufacturers can minimize lead times, reduce idle capacity, and maximize the efficiency of equipment and labor resources.
Compliance and Traceability: In the highly regulated field of medical manufacturing, compliance with quality standards and traceability requirements is non-negotiable. Integration between PlanetTogether and ERP/MES systems ensures end-to-end visibility and traceability, facilitating compliance with regulatory mandates and quality management standards.
Continuous Improvement: Integrated systems support a culture of continuous improvement by providing actionable insights derived from real-time data analytics. Purchasing Managers can identify bottlenecks, analyze production trends, and implement corrective actions to enhance overall operational efficiency and drive continuous yield improvement.
In the competitive landscape of medical manufacturing, production yield optimization is a strategic imperative for ensuring profitability, quality, and regulatory compliance. By harnessing the power of integration between advanced planning tools like PlanetTogether and leading ERP, SCM, and MES systems, Purchasing Managers can drive significant improvements in operational efficiency and yield optimization.
The synergy between PlanetTogether and platforms such as SAP, Oracle, Microsoft Dynamics, Kinaxis, Aveva, and others unlocks new possibilities for streamlining production processes, enhancing visibility, and fostering continuous improvement. As medical manufacturers navigate the complexities of the industry, integrated systems offer a pathway to sustainable growth, innovation, and excellence in patient care.
Are you ready to take your manufacturing operations to the next level? Contact us today to learn more about how PlanetTogether can help you achieve your goals and drive success in your industry.