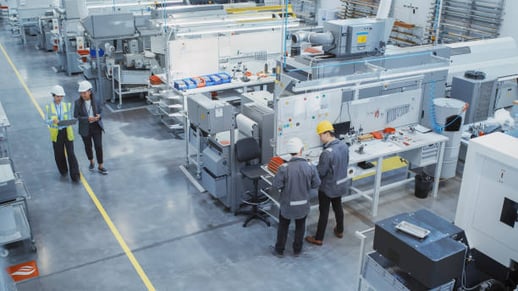
Reshoring and Regionalization in Chemical Manufacturing: How APS and ERP Integration Enable Agile Plant Operations
A Strategic Shift Toward Localized Production
Chemical manufacturing is undergoing a transformation. After decades of globalizing production in search of lower costs, the industry is now pivoting toward reshoring and regionalization—returning production closer to end markets to mitigate risk, reduce lead times, and improve supply chain resilience. For plant managers, this shift isn't just theoretical; it has real implications for day-to-day operations, requiring changes in workforce allocation, raw material sourcing, production scheduling, and asset utilization.
The success of this transition hinges on how well chemical plants can realign operations with dynamic regional demands. Advanced Planning and Scheduling (APS) systems such as PlanetTogether, especially when integrated with enterprise resource planning platforms like SAP, Oracle, Microsoft Dynamics, Kinaxis, or Aveva, offer the digital foundation to support this shift effectively.
Why Reshoring and Regionalization Are Gaining Momentum
Several converging factors are accelerating reshoring and regional production strategies in the chemical sector:
Geopolitical instability and tariffs that disrupt international trade flows.
Sustainability mandates pushing for reduced carbon footprints and localized logistics.
Supply chain disruptions (e.g., COVID-19, the Suez Canal blockage) exposing vulnerabilities in global networks.
Customer demand for responsiveness, especially in specialty chemicals, requiring faster delivery and more flexibility.
Incentives from governments encouraging domestic or regional production of critical materials.
For plant managers, these macro trends translate into a clear mandate: operate more flexibly, scale capacity locally, and align production plans with regional market fluctuations.
Operational Challenges in the Reshoring Transition
Moving toward regional production models is not a simple relocation exercise. It introduces a new layer of complexity in plant operations:
Capacity balancing across multiple facilities in different regions.
Redesigning production scheduling to match localized demand variability.
Managing procurement for regionally available raw materials.
Reconfiguring product lines to match regional regulatory standards.
Maintaining cost-efficiency while avoiding overproduction or idle resources.
These challenges cannot be met with spreadsheets or legacy systems alone. They require interconnected, intelligent planning systems that provide real-time visibility and responsiveness.
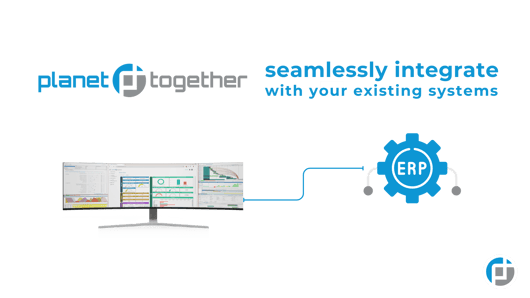
How PlanetTogether + ERP Integration Enables Success
PlanetTogether APS is purpose-built to address the real-time scheduling and resource optimization needs of chemical plants. When integrated with ERP systems like SAP, Oracle, Microsoft Dynamics, Kinaxis, or Aveva, the solution delivers a unified ecosystem where strategic and operational decisions are seamlessly connected.
Real-Time Visibility Across Regional Plants
Integration allows plant managers to:
Compare capacity and workload across multiple facilities.
Visualize production bottlenecks or underutilized assets.
Evaluate alternative scenarios for load sharing or rerouting jobs.
For example, a plant manager overseeing facilities in the U.S. and Germany can instantly determine which location can better absorb a spike in demand for a specialty polymer—without relying on delayed spreadsheets or isolated data.
Optimized Resource Capacity Planning
With integrated APS and ERP, you can align finite scheduling with actual resource constraints:
Personnel availability.
Shift calendars.
Maintenance schedules.
Equipment capabilities.
This level of detail ensures that reshoring doesn’t just shift the burden, but truly optimizes production in the new regional context.
Material Synchronization Across Supply Nodes
When reshoring, you may be dealing with new local suppliers, different lead times, and fluctuating inventory availability. Integration ensures:
Material availability is synchronized with the production schedule.
Shortages and surpluses are flagged before they impact delivery.
Supplier performance data (from ERP) is factored into scheduling (via APS).
This allows you to ensure raw materials are available just-in-time, avoiding both stockouts and costly overstocking.
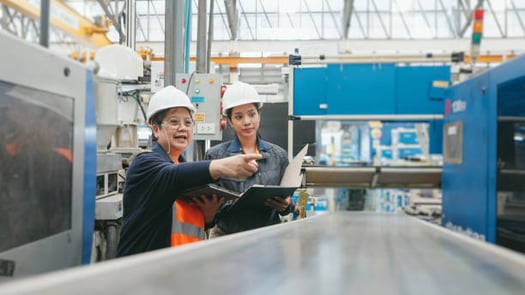
Empowering the Plant Manager’s Role in Strategic Growth
Plant managers are no longer just operations overseers; they are strategic enablers in the reshoring movement. By leveraging integrated APS and ERP systems, they gain:
Decision agility—quickly reacting to regional demand changes.
Execution alignment—translating strategy into real-time floor-level scheduling.
Operational transparency—clear insight into capacity, availability, and constraints.
Cross-functional collaboration—seamless integration with finance, procurement, logistics, and quality teams.
This shift transforms the plant from a static production center to a dynamic, responsive asset in the company’s competitive arsenal.
Digital Readiness for Regional Supply Chains
Reshoring and regionalization in chemical manufacturing are not just temporary trends—they represent a fundamental redesign of how value is created and delivered. For plant managers, the transition brings both opportunity and responsibility.
Success requires tools that go beyond visibility. It requires integrated intelligence—systems that connect ERP-level decisions with plant-floor execution in real time. Solutions like PlanetTogether, when combined with SAP, Oracle, Microsoft Dynamics, Kinaxis, or Aveva, empower plant managers to operate resilient, efficient, and agile regional production networks.
Are you ready to take your manufacturing operations to the next level? Contact us today to learn more about how PlanetTogether can help you achieve your goals and drive success in your industry.
In a reshored future, the best-prepared plants won’t just make chemicals—they’ll make strategic impact.