Resource Allocation for Multi-Product Lines
The ability to efficiently allocate resources across multi-product lines is crucial for success in Food and Beverage manufacturing. Manufacturing IT plays a pivotal role in achieving this efficiency by harnessing the power of advanced planning and scheduling tools. One such tool, PlanetTogether, has gained prominence for its ability to streamline resource allocation.
In this blog, we will explore the challenges faced by Food and Beverage manufacturers in resource allocation and how integration between PlanetTogether and ERP, SCM, and MES systems like SAP, Oracle, Microsoft, Kinaxis, and Aveva can be a game-changer.
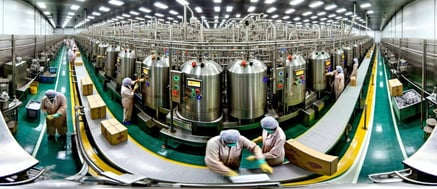
The Complex World of Food and Beverage Manufacturing
Food and Beverage manufacturing is a complex industry characterized by an array of product variations, seasonal demand fluctuations, and stringent quality and safety regulations. Manufacturers in this sector constantly grapple with the challenge of optimizing resources to meet these demands while ensuring efficiency and profitability.
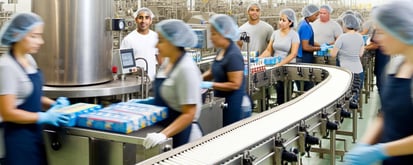
Multi-Product Line Manufacturing
Many Food and Beverage manufacturers operate multiple product lines to cater to diverse customer preferences and market demands. These product lines often require different raw materials, processing equipment, and packaging, making resource allocation a multifaceted challenge. Balancing the production of various products efficiently is vital for maintaining competitiveness in the market.
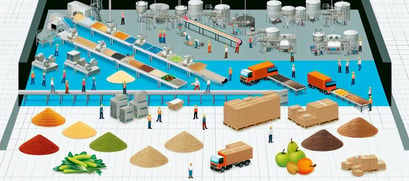
Challenges in Resource Allocation
Dynamic Demand Fluctuations: Seasonal trends, changing consumer preferences, and unforeseen events can lead to sudden and unpredictable shifts in demand for different products.
Resource Constraints: Limited availability of resources such as raw materials, equipment, and labor can impede efficient production across multiple product lines.
Quality Control: Maintaining consistent product quality while switching between different products is a major concern in Food and Beverage manufacturing.
Waste Reduction: Reducing waste and optimizing the use of resources are crucial for sustainability and cost savings.
Compliance and Traceability: Meeting regulatory requirements and ensuring traceability for food safety are paramount in the industry.
The Role of Advanced Planning and Scheduling
To address these challenges, many Food and Beverage manufacturers have turned to advanced planning and scheduling (APS) solutions like PlanetTogether. APS software uses algorithms and data analytics to optimize resource allocation and production scheduling, ultimately improving operational efficiency and profitability.

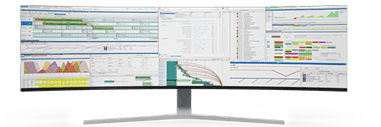
Introducing PlanetTogether
PlanetTogether is a leading APS solution that offers a comprehensive set of features tailored to the needs of Food and Beverage manufacturers. Its core capabilities include:
Finite Capacity Scheduling: Efficiently allocate resources by considering the capacity constraints of equipment, labor, and materials.
Multi-Objective Optimization: Balance conflicting objectives like minimizing lead times, reducing costs, and maximizing resource utilization.
What-If Analysis: Simulate different production scenarios to make informed decisions and adapt to changing circumstances.
Real-Time Monitoring: Monitor production progress in real-time, allowing for quick adjustments to any disruptions.
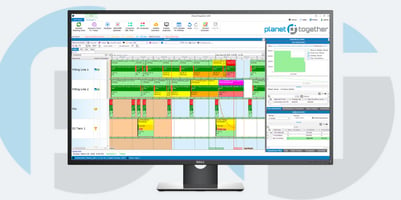
Integration with ERP, SCM, and MES Systems
While PlanetTogether is a powerful tool on its own, its true potential is realized when integrated with other systems such as Enterprise Resource Planning (ERP), Supply Chain Management (SCM), and Manufacturing Execution Systems (MES). Let's explore how this integration can benefit Food and Beverage manufacturers.
SAP Integration
SAP is a widely used ERP system in the manufacturing industry. By integrating PlanetTogether with SAP, manufacturers can achieve seamless data exchange between production planning and business processes. Key benefits include:
Real-Time Data Sync: Ensure that production schedules are always aligned with business priorities and customer demands.
Improved Inventory Management: Optimize stock levels and reduce carrying costs through accurate demand forecasting.
Enhanced Order Fulfillment: Meet customer expectations by ensuring on-time deliveries.
Oracle Integration
Oracle offers a comprehensive suite of business software, including ERP and SCM solutions. Integrating PlanetTogether with Oracle can offer several advantages:
End-to-End Visibility: Gain insights into the entire supply chain, from raw materials to finished products, for better decision-making.
Demand Sensing: Utilize real-time data to sense changes in demand patterns and respond proactively.
Cost Reduction: Identify cost-saving opportunities by optimizing production schedules and resource utilization.
Microsoft Integration
Microsoft offers a range of tools, including Dynamics 365, that can be integrated with PlanetTogether to enhance manufacturing processes. Benefits include:
Seamless Collaboration: Improve communication and collaboration across different departments within the organization.
Predictive Maintenance: Use data analytics to predict equipment failures and schedule maintenance proactively, minimizing downtime.
Scalability: Easily scale production operations to meet growing demand without disrupting existing processes.
Kinaxis Integration
Kinaxis specializes in supply chain management and optimization solutions. Integrating PlanetTogether with Kinaxis can lead to:
Supply Chain Resilience: Adapt quickly to supply chain disruptions and ensure continuity of operations.
Scenario Analysis: Evaluate the impact of different scenarios on resource allocation and production schedules.
Reduced Lead Times: Optimize lead times to meet customer expectations and reduce carrying costs.
Aveva Integration
Aveva offers MES solutions designed to enhance manufacturing operations. Integration with PlanetTogether can result in:
Real-Time Production Data: Access accurate and up-to-date information on production processes.
Quality Control: Implement robust quality control measures to maintain product consistency.
Regulatory Compliance: Ensure adherence to industry-specific regulations and standards.
In the highly competitive Food and Beverage manufacturing industry, resource allocation for multi-product lines is a formidable challenge. However, by harnessing the power of advanced planning and scheduling tools like PlanetTogether and integrating them with ERP, SCM, and MES systems such as SAP, Oracle, Microsoft, Kinaxis, and Aveva, manufacturers can gain a significant advantage.
Efficient resource allocation not only leads to cost savings and improved profitability but also ensures that customer demands are met consistently. It also enhances quality control, regulatory compliance, and sustainability efforts. As the industry continues to evolve, embracing these technologies and integrations will be the key to staying ahead of the curve in Food and Beverage manufacturing.
By investing in the right technology and partnerships, manufacturers can transform their operations, adapt to changing market conditions, and thrive in an increasingly complex and demanding environment.
Are you ready to take your manufacturing operations to the next level? Contact us today to learn more about how PlanetTogether can help you achieve your goals and drive success in your industry.