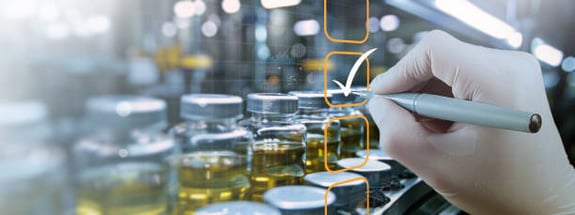
Adapting to Fluctuating Product Demands in Chemical Manufacturing: How APS Integration Enhances Agility and Control
Fluctuating product demand is a persistent challenge in chemical manufacturing, where variability in customer orders, raw material availability, regulatory constraints, and market shifts can quickly destabilize production plans. For Operations Directors navigating this complex landscape, responsiveness and operational agility are essential for maintaining performance and profitability.
The stakes are high. Demand unpredictability in chemical manufacturing doesn’t just result in excess inventory or missed delivery windows—it can cascade into costly shutdowns, compliance violations, and lost customer trust. The solution? Leveraging advanced planning and scheduling (APS) technologies like PlanetTogether, integrated with enterprise systems such as SAP, Oracle, Microsoft Dynamics, Kinaxis, or Aveva, to create a responsive, connected, and optimized production ecosystem.
This blog explores how Operations Directors in chemical manufacturing can address demand fluctuations through integrated APS platforms that provide visibility, simulation, optimization, and real-time adjustments.
The Nature of Demand Volatility in Chemical Manufacturing
In the chemical industry, demand fluctuations stem from several key drivers:
Market Seasonality: Demand for certain chemicals peaks during specific seasons—agricultural chemicals before planting seasons, for example.
Regulatory Changes: New environmental or safety regulations can abruptly affect product formulations or limit output.
Raw Material Supply Disruptions: The global sourcing of feedstocks makes chemical production vulnerable to geopolitical tensions and logistical delays.
Customer Order Variability: Many chemical manufacturers serve diverse customers across industries, creating inconsistency in order sizes, timelines, and priorities.
Innovation and R&D: Product development cycles and customer specifications can rapidly shift based on new applications or performance requirements.
Traditional planning methods, often built around spreadsheets or legacy ERP systems, are ill-equipped to deal with this complexity. They lack the flexibility, speed, and intelligence required for real-time scenario planning and decision-making.
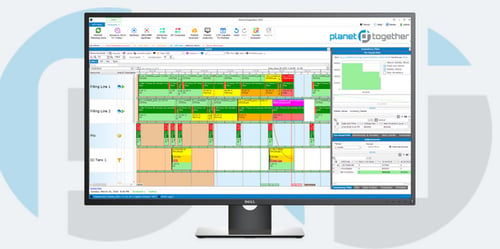
How APS Helps Navigate Demand Volatility
Advanced Planning and Scheduling (APS) systems are designed to tackle exactly this type of complexity. PlanetTogether APS, when integrated with ERP platforms like SAP, Oracle, Microsoft Dynamics, Kinaxis, or Aveva, enables chemical manufacturers to:
Gain Real-Time Visibility
With PlanetTogether’s integration into existing ERP infrastructure, Operations Directors gain immediate visibility into all aspects of production—inventory, capacity, labor availability, material requirements, and order status. For instance, connecting to SAP allows real-time data exchange between planning and procurement, ensuring material readiness aligns with shifting demand patterns.
Model Scenarios and Simulate Outcomes
APS enables “what-if” simulations to evaluate the impact of demand surges, material shortages, or production delays. Operations Directors can run scenarios such as:
What if demand for a solvent increases by 30% next quarter?
What if our primary supplier experiences a two-week delay?
What if we allocate production across two different plants?
These simulations allow leaders to make informed decisions grounded in data rather than gut instinct.
Optimize Production Schedules
PlanetTogether automatically generates optimized schedules based on constraints and business rules. This is crucial in chemical manufacturing, where batch sequencing, cleaning time, hazardous material segregation, and equipment availability must be meticulously considered. Integration with systems like Aveva or Microsoft Dynamics provides up-to-date asset status, minimizing the risk of scheduling conflicts or underutilized resources.
React to Demand Shifts in Real Time
With real-time synchronization between APS and ERP systems, updates to demand forecasts or customer orders are instantly reflected in the production plan. If a large customer suddenly moves up their delivery date, or if an unexpected order is placed, the Operations Director can quickly assess feasibility and reoptimize the schedule—without disrupting overall plant performance.
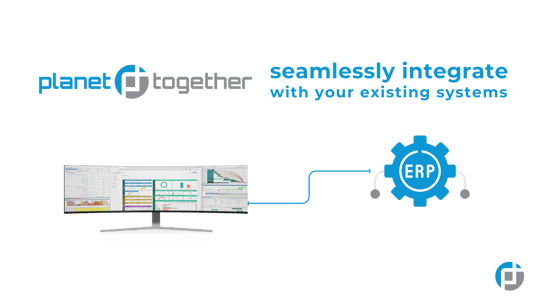
Integration with ERP and MES: Building a Connected Supply Chain
The power of APS is magnified when integrated into the broader enterprise environment. Here’s how PlanetTogether works synergistically with key systems:
SAP Integration: Aligns production planning with procurement, finance, and warehouse management for a seamless flow of materials and information.
Oracle Integration: Facilitates advanced analytics, demand planning, and cross-functional collaboration through a unified data architecture.
Microsoft Dynamics Integration: Streamlines order management, customer service, and inventory control alongside production planning.
Kinaxis Integration: Enhances supply chain agility and connects production plans with broader supply chain strategies and demand forecasts.
Aveva Integration: Bridges APS with manufacturing execution systems (MES), ensuring that scheduling decisions are grounded in real-time machine and plant-level data.
For an Operations Director, these integrations transform APS from a siloed planning tool into a command center for proactive decision-making.
Key Benefits for Chemical Manufacturing Operations
Improved Agility
Quickly replan production in response to changing market conditions or customer demands without compromising efficiency.
Increased Throughput
By eliminating bottlenecks and minimizing downtime, APS ensures that capacity is fully utilized—even under unpredictable conditions.
Enhanced Collaboration
With APS integrated into ERP and MES systems, all stakeholders—from procurement to shop floor operators—are aligned and informed.
Better Compliance
APS helps schedule production runs that comply with regulations for handling hazardous chemicals, batch traceability, and cleaning procedures.
Reduced Waste
Smarter scheduling prevents overproduction, reduces expired inventory, and limits raw material waste.
Fluctuating product demand doesn’t have to disrupt your production goals. By adopting a responsive, integrated planning approach, Operations Directors in chemical manufacturing can turn volatility into a competitive advantage. With PlanetTogether APS driving synchronized, optimized, and agile decision-making—your operations can remain resilient, efficient, and ready for whatever the market throws your way.
Investing in an integrated planning ecosystem with PlanetTogether APS, connected to ERP and MES platforms like SAP, Oracle, Microsoft Dynamics, Kinaxis, or Aveva, equips your facility with the tools needed to navigate uncertainty, optimize performance, and seize emerging opportunities.
Are you ready to take your manufacturing operations to the next level? Contact us today to learn more about how PlanetTogether can help you achieve your goals and drive success in your industry.