Adaptive Production Line Balancing
The role of a Production Scheduler is pivotal in ensuring smooth operations and meeting customer demands. With ever-changing market trends, fluctuating raw material prices, and evolving consumer preferences, the need for adaptive production line balancing has never been more crucial.
In this blog, we'll look into the concept of adaptive production line balancing and how it can revolutionize efficiency in food and beverage manufacturing facilities. Additionally, we'll explore the integration between PlanetTogether, a leading production scheduling software, and various ERP, SCM, and MES systems such as SAP, Oracle, Microsoft, Kinaxis, and Aveva, to streamline operations and drive optimization.
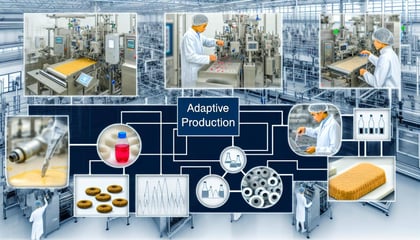
Understanding Adaptive Production Line Balancing
Traditionally, production line balancing involved static allocation of resources and predefined schedules. However, in today's fast-paced environment, this approach often falls short in meeting the demands of modern manufacturing. Adaptive production line balancing, on the other hand, embraces flexibility and responsiveness to dynamic factors such as demand fluctuations, equipment downtime, and resource constraints.
At its core, adaptive production line balancing focuses on optimizing the allocation of resources, including manpower, machinery, and materials, in real-time to maximize efficiency and minimize waste. It leverages advanced algorithms and predictive analytics to anticipate disruptions and proactively adjust production schedules accordingly.
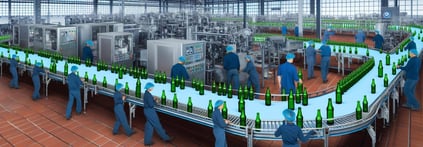
Benefits of Adaptive Production Line Balancing
Improved Efficiency: By dynamically allocating resources based on real-time data and demand signals, adaptive production line balancing minimizes idle time and maximizes throughput, leading to enhanced operational efficiency.
Enhanced Agility: In today's volatile market landscape, agility is key to staying competitive. Adaptive production line balancing enables manufacturers to quickly respond to changes in demand, supply, or production conditions, ensuring timely delivery and customer satisfaction.
Reduced Costs: Optimizing resource utilization and minimizing downtime translates into cost savings for food and beverage manufacturers. By eliminating inefficiencies and waste, adaptive production line balancing helps optimize operational costs without compromising on quality.
Better Decision Making: Integrated with advanced analytics and reporting capabilities, adaptive production line balancing provides actionable insights into production performance, allowing production schedulers to make informed decisions and drive continuous improvement initiatives.
Integration with PlanetTogether and ERP/SCM/MES Systems
One of the critical success factors in implementing adaptive production line balancing is seamless integration between production scheduling software like PlanetTogether and enterprise systems such as ERP (Enterprise Resource Planning), SCM (Supply Chain Management), and MES (Manufacturing Execution Systems). Let's explore how this integration adds value to food and beverage manufacturing operations:
Real-time Data Exchange: Integration between PlanetTogether and ERP/SCM/MES systems facilitates real-time data exchange, enabling production schedulers to access up-to-date information on inventory levels, production orders, and resource availability. This ensures accurate scheduling and efficient resource allocation.
Streamlined Workflows: By automating data transfer and synchronization between different systems, integration eliminates manual data entry and reduces the risk of errors. This streamlines workflows and enhances collaboration between production, planning, and procurement departments.
Comprehensive Visibility: With integrated systems, production schedulers gain comprehensive visibility into end-to-end production processes, from order placement to delivery. This visibility enables proactive decision-making and helps identify bottlenecks or inefficiencies for timely resolution.
Predictive Analytics: Leveraging data from integrated systems, production scheduling software can employ predictive analytics to forecast demand, optimize inventory levels, and anticipate production constraints. This proactive approach empowers production schedulers to mitigate risks and optimize resource utilization.
In the competitive landscape of food and beverage manufacturing, adaptive production line balancing emerges as a game-changer, enabling manufacturers to optimize efficiency, enhance agility, and reduce costs. By leveraging advanced production scheduling software like PlanetTogether and integrating with ERP, SCM, and MES systems, production schedulers can orchestrate seamless and agile production processes that meet the demands of today's dynamic market.
As you navigate the complexities of production scheduling in your food and beverage manufacturing facility, embracing adaptive production line balancing can unlock new opportunities for growth, innovation, and competitive advantage. By harnessing the power of technology and integration, you can steer your operations towards greater efficiency, resilience, and success in the ever-evolving landscape of modern manufacturing.
Are you ready to take your manufacturing operations to the next level? Contact us today to learn more about how PlanetTogether can help you achieve your goals and drive success in your industry.