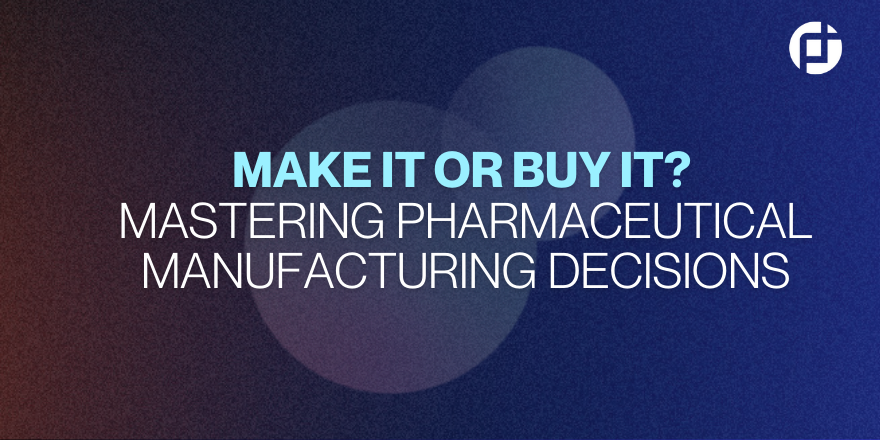
In the realm of pharmaceutical manufacturing, efficiency and cost-effectiveness are paramount. Purchasing Managers play a pivotal role in ensuring that the production processes run smoothly while keeping expenses in check. One crucial decision they often face is whether to make certain components or products in-house or to outsource them to external vendors. This decision, known as the make-or-buy decision, requires careful analysis and consideration of various factors.
In this blog, we'll look into the intricacies of make-or-buy decisions in pharmaceutical production, and how integration between PlanetTogether and ERP, SCM, and MES systems can streamline the process.
Understanding Make-or-Buy Decisions
Make-or-buy decisions involve weighing the costs and benefits of producing an item internally versus purchasing it from an external supplier. In pharmaceutical manufacturing, these decisions can range from manufacturing active pharmaceutical ingredients (APIs) to outsourcing packaging and labeling services. Several factors influence these decisions, including cost, quality, capacity, expertise, and strategic alignment.
Factors Influencing Make-or-Buy Decisions
Cost Analysis
-
- Direct Costs: Purchasing raw materials, labor, equipment, and overhead costs associated with in-house production.
- Indirect Costs: Quality control, regulatory compliance, maintenance, and facility expenses.
- Supplier Costs: Evaluating the pricing and terms offered by external vendors.
Quality and Compliance
- Compliance Requirements: Adherence to Good Manufacturing Practices (GMP) and regulatory standards.
- Quality Control: Ensuring consistency, purity, and safety of the final product.
Capacity and Expertise
- In-house Capacity: Assessing available resources and production capabilities.
- External Expertise: Leveraging specialized knowledge and capabilities of external vendors.
Strategic Considerations
- Core Competencies: Focusing on areas where the company possesses expertise and competitive advantage.
- Risk Mitigation: Diversifying suppliers to minimize dependency and mitigate supply chain risks.
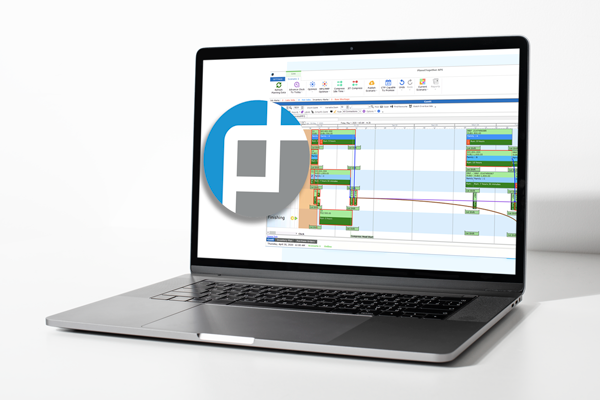
Integration of PlanetTogether with ERP, SCM, and MES Systems
PlanetTogether is a powerful production planning and scheduling software that optimizes manufacturing processes. Integration with ERP, SCM, and MES systems enhances its functionality and provides a holistic view of the supply chain. Here's how integration benefits make-or-buy decisions:
Data Synchronization
-
- Seamless Integration: Real-time exchange of data between PlanetTogether and ERP systems like SAP, Oracle, or Microsoft ensures accurate inventory levels, production schedules, and procurement requirements.
- Supply Chain Visibility: Access to up-to-date information on raw material availability, lead times, and supplier performance enables informed decision-making.
Enhanced Planning Capabilities
- Scenario Analysis: PlanetTogether's advanced planning algorithms combined with ERP data allow Purchasing Managers to simulate various production scenarios and evaluate their impact on costs, lead times, and resource utilization.
- Demand Forecasting: Integration with SCM systems enables forecasting of demand fluctuations, helping in determining optimal production quantities and inventory levels.
Streamlined Procurement Processes
- Automated Replenishment: Integration with ERP and SCM systems automates procurement processes, triggering purchase orders based on predefined inventory thresholds, production schedules, and demand forecasts.
- Vendor Management: MES integration facilitates tracking of supplier performance metrics such as on-time delivery, quality, and compliance, aiding in supplier selection and contract negotiations.
Real-time Monitoring and Analysis
- Performance Metrics: PlanetTogether's integration with MES systems allows real-time monitoring of production metrics such as cycle times, throughput, and yield rates, enabling continuous improvement initiatives and cost optimization.
- KPI Tracking: Seamless data flow between PlanetTogether and ERP systems enables tracking of key performance indicators (KPIs) such as cost per unit, inventory turnover, and production efficiency, facilitating better decision-making.
In the landscape of pharmaceutical manufacturing, make-or-buy decisions play a crucial role in optimizing costs, mitigating risks, and enhancing competitiveness. Purchasing Managers must leverage advanced technologies such as PlanetTogether integrated with ERP, SCM, and MES systems to make informed decisions that align with strategic objectives.
By conducting thorough cost analyses, evaluating quality and compliance requirements, assessing capacity and expertise, and leveraging real-time data and analytics, pharmaceutical companies can maximize efficiency and profitability in their production processes.
Through strategic integration and collaboration across the supply chain, the pharmaceutical industry can navigate challenges and capitalize on opportunities in an increasingly complex global market.