Bottlenecks can hinder production in a variety of ways. Whether it is meeting maximum potential, increasing efficiency, or attempting to generate a certain amount of product within a specified timeframe, bottlenecks could be the number one obstacle that is standing in the way. This is why many manufacturing facilities find themselves investing in locating ways to eliminate or reduce production bottlenecks. This could be done through various methodologies, with lean concepts and tools being at the top of the list that can aid with this aspect.
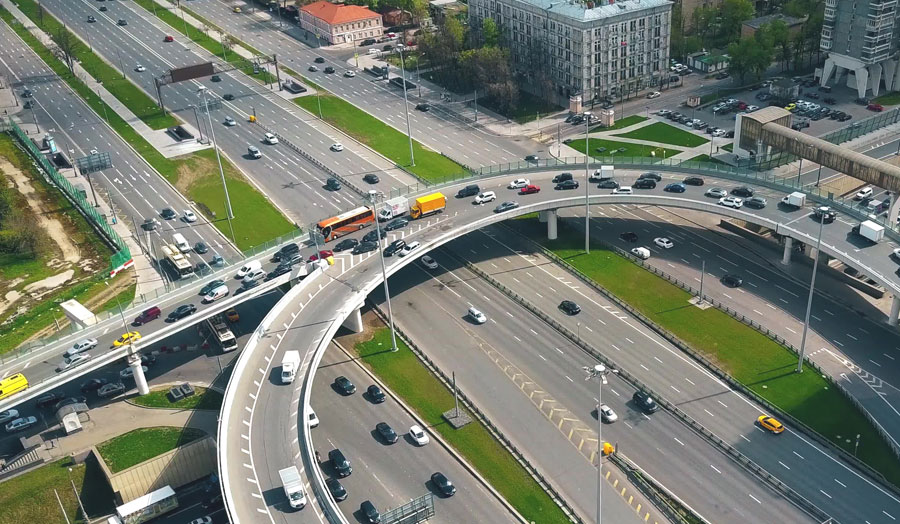
Eliminating production bottlenecks through lean concepts and tools are one of the most advantageous methods to eliminating bottlenecks. It is essential to understand these concepts and look at your manufacturing facility from a lean perspective. When using lean methods, utilizing certain steps and procedures can help with avoiding production bottlenecks. Therefore, within this blog we are going to discuss the lean methods that can be used to contain and avoid production bottlenecks.
Lean Methods and Production Bottlenecks: How to Avoid Them
These two steps and procedures pertaining to lean methods and production bottlenecks pertain to following:
- Identify Bottlenecks – First and foremost, it is a must to locate and identify the bottleneck. This can be done in a series of ways, which may include timing equipment or tasks, Kanban tables, etc. You can look into the entire process as a whole and take a look into if customers, equipment, or the supply chain is the bottleneck. Are suppliers taking too long and not delivering on time? Is your equipment not functioning correctly and taking longer than needed due to poor maintenance? Are customers changing engineering specifications on particular products and slowing part shipping? All of these are prevalent questions to ask yourself when attempting to locate the bottleneck. Ultimately, it will be the longest process and what seems to have the most time. Once the bottleneck is identified, it is now time to start looking to ways that the bottleneck can be reduced or eliminated.
- Reduce Bottleneck Impact – When attempting to reduce the bottleneck impact, there are various ways that this can be conducted. This includes process improvement, adding capacity, automating the process, or subcontracting work. It really depends on each facility and what exactly needs to be conducted, but reducing the bottleneck can potentially be conducted through process improvement strategies. If you have employees that are the bottleneck, then take a look into their process and see what seems to be taking the most time. If it is equipment, see if there are ways that you can make the equipment function more efficiently. There are a variety of ways that bottlenecks can be reduced and lean tools can be particularly beneficial.
A software that can help with production bottlenecks includes PlanetTogether’s Advanced Planning and Scheduling (APS) Software. Advanced Planning and Scheduling (APS) Software can boost operational efficiency and ultimately take production up a notch through cost reduction, profitability increase, and ultimately operational enhancement.
Advanced Planning and Scheduling Software
Advanced Planning and Scheduling (APS) software has become a must for modern-day manufacturing operations due to customer demand for increased product mix and fast delivery combined with downward cost pressures. APS can be quickly integrated with a ERP/MRP software to fill gaps where these system lack planning and scheduling flexibility and accuracy. Advanced Planning and Scheduling (APS) helps planners save time while providing greater agility in updating ever-changing priorities, production schedules, and inventory plans.
- Create optimized schedules balancing production efficiency and delivery performance
- Maximize output on bottleneck resources to increase revenue
- Synchronize supply with demand to reduce inventories
- Provide company-wide visibility to capacity
- Enable scenario data-driven decision making
Implementation of Advanced Planning and Scheduling (APS) software will take your manufacturing operations to the next level of production efficiency, taking advantage of the operational data you already have in your ERP.
Related What If Video
APS Resources