Harnessing Continuous Improvement Through Scheduling Feedback Loops
Optimizing production schedules is crucial for meeting demand, ensuring efficiency, and maintaining quality standards in food and beverage manufacturing. The integration of advanced scheduling software like PlanetTogether with enterprise resource planning (ERP), supply chain management (SCM), and manufacturing execution systems (MES) such as SAP, Oracle, Microsoft, Kinaxis, Aveva, and others has revolutionized the way manufacturers operate.
This integration paves the way for continuous improvement through scheduling feedback loops, enabling companies to adapt quickly to changing market conditions, minimize waste, and enhance overall performance.
In this blog, we look into the significance of scheduling feedback loops in the context of food and beverage manufacturing and how the integration of cutting-edge technologies facilitates this process.
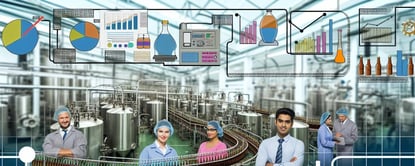
The Concept of Scheduling Feedback Loops
Scheduling feedback loops involve the cyclical process of generating schedules, executing them, gathering data on performance, analyzing this data, and using insights to refine and improve future schedules. It's a continuous iterative process aimed at achieving optimal production efficiency and resource utilization. In the realm of food and beverage manufacturing, where factors such as perishability, seasonality, and fluctuating consumer demand play a significant role, the ability to adapt and optimize schedules in real-time is paramount.
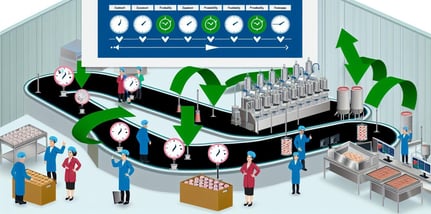
Benefits of Scheduling Feedback Loops in Food and Beverage Manufacturing
Improved Efficiency: By continuously analyzing production data and performance metrics, manufacturers can identify bottlenecks, optimize production sequences, and allocate resources more effectively. This leads to enhanced overall efficiency and throughput.
Reduced Waste: Efficient scheduling minimizes the risk of overproduction, excess inventory, and wastage of raw materials. By aligning production schedules closely with demand forecasts and inventory levels, manufacturers can mitigate the risk of obsolete or expired products, thereby reducing waste and maximizing profitability.
Enhanced Quality Control: Timely scheduling adjustments allow manufacturers to maintain stringent quality control standards throughout the production process. By ensuring that resources are allocated optimally and production flows smoothly, scheduling feedback loops contribute to consistently high-quality products that meet customer expectations.
Greater Flexibility and Adaptability: In today's fast-paced market environment, agility is key to staying competitive. Scheduling feedback loops enable manufacturers to respond swiftly to changes in demand, supply chain disruptions, or unexpected production issues. By leveraging real-time data and analytics, companies can make informed decisions and adjust schedules on the fly to minimize downtime and maximize productivity.
Cost Savings: Efficient scheduling leads to cost savings across various aspects of production, including labor, energy consumption, and inventory holding costs. By optimizing resource utilization and streamlining production processes, manufacturers can achieve significant cost reductions while maintaining profitability.
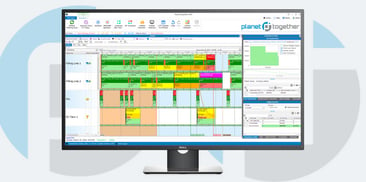
Integration of PlanetTogether with ERP, SCM, and MES Systems
The seamless integration of advanced scheduling software like PlanetTogether with ERP, SCM, and MES systems amplifies the benefits of scheduling feedback loops in food and beverage manufacturing. Let's explore how this integration enhances the efficiency and effectiveness of production scheduling:
Real-time Data Exchange: Integration enables the exchange of real-time data between scheduling software and other enterprise systems, providing up-to-date information on inventory levels, production capacities, order status, and more. This real-time visibility allows for better decision-making and enables faster response to changing conditions.
Streamlined Workflows: By automating data transfer and synchronization between different systems, integration eliminates manual errors and streamlines workflows. This ensures that accurate and consistent data is available across the organization, facilitating smoother collaboration and communication between departments.
Holistic Planning and Optimization: Integrated systems enable holistic planning and optimization across the entire value chain, from production and inventory management to procurement and distribution. This integrated approach ensures that scheduling decisions take into account the broader business objectives and constraints, leading to more robust and resilient supply chain operations.
Advanced Analytics and Reporting: Integration allows for the aggregation of data from multiple sources, enabling advanced analytics and reporting capabilities. Manufacturers can leverage this data to gain deeper insights into production performance, identify trends and patterns, and uncover opportunities for further optimization.
Continuous Improvement: By integrating scheduling software with ERP, SCM, and MES systems, manufacturers establish a closed-loop feedback mechanism that facilitates continuous improvement. Performance data collected from production activities feeds back into the scheduling process, enabling iterative refinement of schedules based on actual performance metrics.
In the highly competitive landscape of food and beverage manufacturing, continuous improvement is not just a goal but a necessity for survival and growth. Scheduling feedback loops, enabled by the integration of advanced scheduling software like PlanetTogether with ERP, SCM, and MES systems, provide manufacturers with the tools and insights needed to drive ongoing optimization and efficiency gains.
By embracing this iterative approach to scheduling, companies can adapt to changing market dynamics, minimize waste, enhance quality, and ultimately, achieve sustainable success in the industry.
Are you ready to take your manufacturing operations to the next level? Contact us today to learn more about how PlanetTogether can help you achieve your goals and drive success in your industry.