Continuous Improvement Initiatives in Industrial Manufacturing
Whether it's optimizing production processes, reducing downtime, or enhancing supply chain efficiency, continuous improvement initiatives are essential in industrial manufacturing. With the advent of advanced manufacturing technologies and digital solutions, companies have powerful tools at their disposal to drive these initiatives forward. In industrial manufacturing, staying competitive requires a relentless pursuit of improvement across all facets of operations.
One such tool is the integration between PlanetTogether, a leading production planning and scheduling software, and enterprise resource planning (ERP) systems such as SAP, Oracle, Microsoft Dynamics, Kinaxis, Aveva, and others. This integration offers manufacturers a seamless flow of data and information between their planning and execution systems, enabling them to streamline operations, make data-driven decisions, and foster a culture of continuous improvement.
In this blog, we'll explore how manufacturing IT professionals can leverage this integration to drive continuous improvement initiatives within their industrial manufacturing facilities.
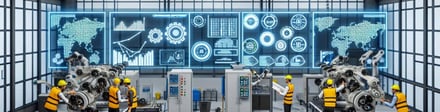
Continuous Improvement Initiatives
Continuous improvement is not a one-time project; rather, it's a mindset and a strategic approach to constantly enhancing processes, products, and services. It involves identifying areas for improvement, implementing changes, measuring outcomes, and then repeating the cycle to drive further enhancements. Continuous improvement initiatives encompass a wide range of activities, including:
Lean Manufacturing: Applying principles such as just-in-time production, waste reduction, and value stream mapping to optimize processes and eliminate inefficiencies.
Six Sigma: Using data-driven methodologies to identify and eliminate defects, thereby improving quality and reducing variation in processes.
Total Productive Maintenance (TPM): Focusing on proactive equipment maintenance to minimize downtime, improve reliability, and extend asset life.
Supply Chain Optimization: Enhancing the efficiency and resilience of the supply chain through better demand forecasting, inventory management, and supplier collaboration.
Employee Empowerment: Engaging employees at all levels of the organization to contribute ideas for improvement and fostering a culture of innovation.

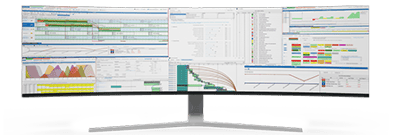
Integration Between PlanetTogether and ERP Systems
Now, let's look into how the integration between PlanetTogether and ERP systems can support these continuous improvement initiatives:
Seamless Data Exchange: By integrating PlanetTogether with ERP systems, manufacturing IT professionals can ensure a seamless exchange of data between production planning and execution. This means that updated production schedules, material requirements, and resource allocations are automatically synchronized between the two systems, eliminating the need for manual data entry and reducing the risk of errors.
Real-Time Visibility: With integrated systems, stakeholders across the organization have real-time visibility into production schedules, inventory levels, and order statuses. This visibility enables proactive decision-making, as managers can quickly identify bottlenecks, allocate resources effectively, and respond promptly to changes in demand or supply.
Optimized Resource Utilization: By leveraging integrated data, manufacturers can optimize resource utilization across their facilities. Whether it's labor, equipment, or materials, having a comprehensive view of resource availability and demand allows companies to allocate resources more efficiently, minimize idle time, and maximize throughput.
Continuous Process Improvement: Integrated systems provide a wealth of data that can be analyzed to identify areas for process improvement. By tracking key performance indicators (KPIs) such as cycle times, setup times, and defect rates, manufacturers can pinpoint inefficiencies and implement targeted improvements to enhance productivity and quality.
Predictive Analytics: With integrated data from both planning and execution systems, manufacturers can harness the power of predictive analytics to anticipate and mitigate potential issues before they occur. Whether it's predicting machine failures, stockouts, or production delays, advanced analytics algorithms can help companies take proactive measures to keep operations running smoothly.
Continuous improvement initiatives are essential for industrial manufacturing companies looking to stay competitive in today's dynamic market. By leveraging integration between PlanetTogether and ERP systems, manufacturing IT professionals can streamline operations, optimize resource utilization, and drive continuous improvement across all facets of their organizations.
Whether it's reducing setup times, improving on-time delivery, or optimizing inventory levels, integrated systems provide the data and insights needed to identify opportunities for improvement and implement targeted solutions.
By embracing a culture of continuous improvement and harnessing the power of integrated technology solutions, manufacturers can position themselves for success in an ever-evolving industry landscape. Are you ready to take your manufacturing operations to the next level? Contact us today to learn more about how PlanetTogether can help you achieve your goals and drive success in your industry.