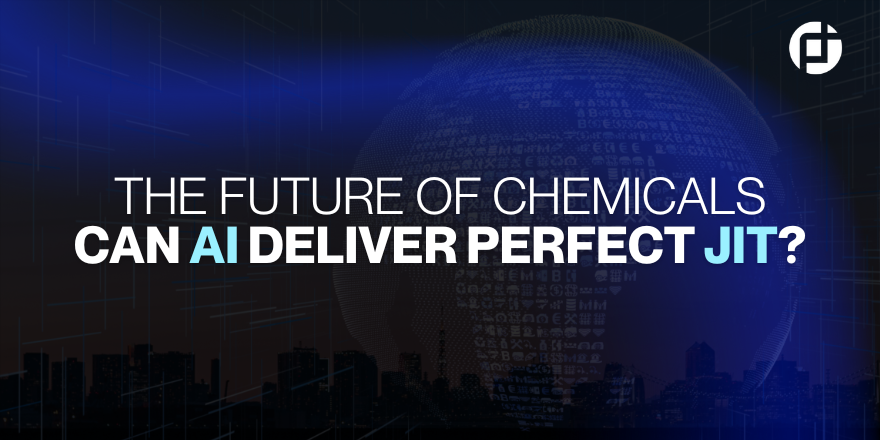
The pursuit of operational excellence is an ongoing challenge for Operations Directors. Just-in-Time (JIT) manufacturing has emerged as a key strategy to optimize efficiency, reduce waste, and enhance overall productivity.
In this blog, we will explore the transformative potential of integrating machine learning models, specifically through the utilization of PlanetTogether, with leading Enterprise Resource Planning (ERP), Supply Chain Management (SCM), and Manufacturing Execution Systems (MES) such as SAP, Oracle, Microsoft, Kinaxis, and Aveva. This integration not only streamlines processes but also propels chemical manufacturing facilities into the era of intelligent, data-driven decision-making.
Understanding Just-in-Time Manufacturing
Just-in-Time manufacturing revolves around the concept of producing goods at the precise moment they are needed in the production process. This methodology is designed to minimize inventory, reduce lead times, and enhance the overall agility of manufacturing operations. Achieving JIT efficiency requires a delicate balance between demand forecasting, production scheduling, and supply chain optimization. This is where the integration of machine learning models becomes a game-changer.
Challenges in Traditional Manufacturing Operations
Before looking into the benefits of machine learning models for JIT manufacturing, it's crucial to acknowledge the challenges faced by Operations Directors in traditional setups. These challenges include:
Inaccurate Demand Forecasting: Traditional forecasting methods often fall short in predicting dynamic market demands accurately.
Production Scheduling Complexity: Coordinating production schedules with fluctuating demand and varying lead times can be a daunting task without advanced tools.
Supply Chain Disruptions: Unforeseen disruptions, whether due to natural disasters or geopolitical events, can cripple the supply chain and impact production timelines.
Waste and Inventory Costs: Excessive inventory and inefficient production processes contribute to increased costs and waste.
Lack of Real-time Visibility: Limited visibility into real-time data hampers the ability to make informed decisions promptly.
The Role of Machine Learning in JIT Manufacturing
Machine learning models, when integrated seamlessly with ERP, SCM, and MES systems, provide a robust solution to address the challenges outlined above. Let's explore the specific benefits of this integration:
Accurate Demand Forecasting
By leveraging historical data, customer behavior patterns, and external factors, machine learning algorithms enhance the accuracy of demand forecasting. This ensures that production schedules align closely with actual market demands, reducing the risk of overproduction or stockouts.
Optimized Production Scheduling
Machine learning algorithms, powered by solutions like PlanetTogether, analyze vast datasets to optimize production schedules. These algorithms consider various factors, including machine availability, labor resources, and production constraints, resulting in streamlined and efficient production processes.
Resilient Supply Chain Management
Integration with SCM systems allows machine learning models to proactively identify potential disruptions in the supply chain. Whether it's a sudden increase in demand or a supply chain bottleneck, these models enable Operations Directors to make informed decisions swiftly, minimizing the impact on production.
Cost Reduction through Waste Minimization
JIT manufacturing aims to minimize waste by producing only what is needed when it is needed. Machine learning models contribute to this goal by identifying opportunities for waste reduction and optimizing inventory levels. This, in turn, leads to significant cost savings.
Real-time Visibility and Decision-Making
The integration of machine learning models provides Operations Directors with real-time visibility into key performance indicators. This enables them to make data-driven decisions promptly, improving overall operational agility and responsiveness.
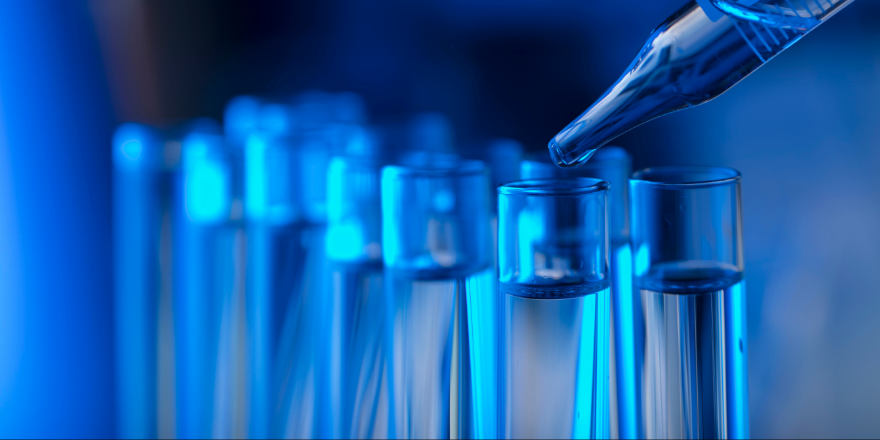
Integration with Leading ERP, SCM, and MES Systems
One of the critical success factors in implementing machine learning for JIT manufacturing is the seamless integration with existing systems. The integration between PlanetTogether and industry-leading systems such as SAP, Oracle, Microsoft, Kinaxis, and Aveva ensures a holistic and synchronized approach to operations. This collaboration enhances data accuracy, eliminates silos, and facilitates a cohesive flow of information across the entire manufacturing ecosystem.
SAP Integration
SAP integration brings together the power of PlanetTogether's machine learning capabilities with SAP's robust ERP functionalities. This synergy results in a unified platform that optimizes resource allocation, enhances visibility, and enables real-time collaboration across the organization.
Oracle Collaboration
By integrating machine learning models with Oracle's SCM and ERP systems, chemical manufacturing facilities can achieve an unparalleled level of precision in demand forecasting, inventory management, and production scheduling. The result is a synchronized and agile supply chain.
Microsoft Dynamics 365 Connectivity
The integration of PlanetTogether with Microsoft Dynamics 365 empowers Operations Directors with a comprehensive solution that combines the strengths of ERP and advanced production scheduling. This collaboration fosters a more adaptive and responsive manufacturing environment.
Kinaxis Harmony
Kinaxis Harmony, known for its agile and responsive supply chain solutions, complements the capabilities of machine learning models integrated through PlanetTogether. This collaboration ensures that chemical manufacturing facilities can proactively adapt to changing market dynamics.
Aveva's MES Integration
The integration of machine learning models with Aveva's Manufacturing Execution System enhances the efficiency of production processes. Real-time data from the MES system, coupled with predictive analytics, enables Operations Directors to make informed decisions for continuous improvement.
The integration of machine learning models for Just-in-Time manufacturing represents a quantum leap in the evolution of chemical manufacturing operations. The synergy between PlanetTogether and leading ERP, SCM, and MES systems is a strategic imperative for Operations Directors seeking to optimize efficiency, reduce costs, and stay ahead in today's competitive landscape.
As technology continues to advance, embracing the potential of machine learning becomes not just a competitive advantage but a necessity for sustained success. The era of intelligent, data-driven decision-making is here, and chemical manufacturing facilities that harness the power of these technologies will undoubtedly lead the way into a more efficient, resilient, and sustainable future.