Sales and Operations Planning (S&OP)
As an Operations Director in an industrial manufacturing facility, you understand the complexities of managing production while meeting customer demands, optimizing resources, and controlling costs. In industrial manufacturing, where efficiency, agility, and precision reign supreme, one key strategy stands out as indispensable: Sales and Operations Planning (S&OP).
In this blog, we look into the significance of S&OP in streamlining operations and achieving organizational success. Moreover, we'll explore how integration between advanced planning tools like PlanetTogether and leading ERP, SCM, and MES systems can revolutionize your approach to S&OP, paving the way for enhanced efficiency and profitability.
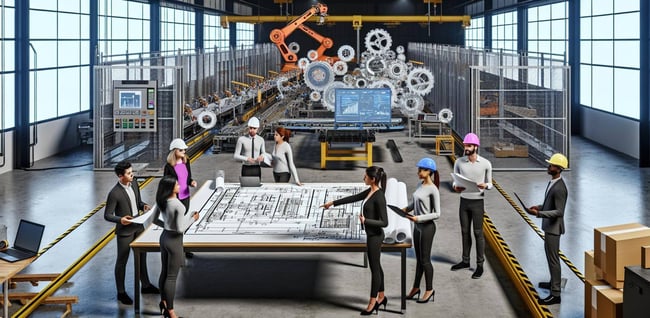
Understanding Sales and Operations Planning (S&OP)
At its core, Sales and Operations Planning (S&OP) is a strategic process that aligns sales forecasts with operational capabilities to optimize resource allocation, minimize costs, and maximize customer satisfaction. It serves as a bridge between sales and production, enabling seamless coordination across various departments within an organization. By integrating sales forecasts, production schedules, inventory levels, and resource capacities, S&OP empowers decision-makers to make informed choices that drive business growth while mitigating risks.
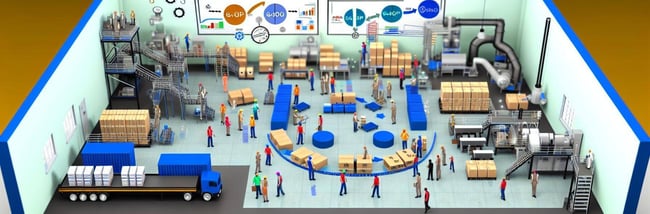
S&OP in Industrial Manufacturing
In the realm of industrial manufacturing, where production cycles are intricate and lead times can vary significantly, S&OP plays a pivotal role in ensuring operational excellence. Here's how:
Demand Forecasting and Capacity Planning: S&OP allows operations directors to anticipate market demand accurately and align production capacities accordingly. By integrating historical sales data, market trends, and customer insights, S&OP facilitates informed decision-making regarding resource allocation and capacity planning. This proactive approach minimizes the risk of overstocking or stockouts, optimizing inventory levels and enhancing customer satisfaction.
Production Scheduling and Optimization: With S&OP, industrial manufacturing facilities can develop robust production schedules that balance demand fluctuations with resource constraints. By synchronizing production activities with sales forecasts and inventory targets, operations directors can optimize equipment utilization, reduce setup times, and minimize production bottlenecks. This agile approach enhances manufacturing efficiency, shortens lead times, and enables prompt response to changing market dynamics.
Supply Chain Integration and Collaboration: In today's interconnected business environment, seamless collaboration across the supply chain is paramount. S&OP facilitates integration between suppliers, manufacturers, and distributors, enabling real-time visibility into inventory levels, order status, and delivery schedules. By aligning supply chain activities with sales forecasts and production plans, operations directors can minimize supply chain disruptions, enhance supplier reliability, and improve overall responsiveness to customer demands.

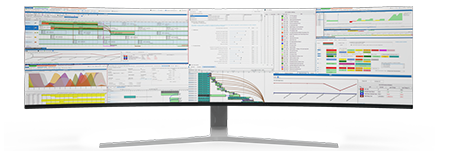
Integration between PlanetTogether and Leading ERP, SCM, and MES Systems
While the benefits of S&OP are undeniable, unlocking its full potential requires robust planning tools and seamless integration with enterprise systems. PlanetTogether, a leading advanced planning and scheduling software, offers unparalleled capabilities for optimizing production processes and enhancing decision-making.
When integrated with leading ERP, SCM, and MES systems such as SAP, Oracle, Microsoft, Kinaxis, and Aveva, PlanetTogether enables operations directors to achieve greater synergy between sales, operations, and supply chain management.
Here's how integration between PlanetTogether and ERP, SCM, and MES systems revolutionizes S&OP:
Real-Time Data Exchange: Integration between PlanetTogether and ERP, SCM, and MES systems facilitates seamless data exchange, ensuring that sales forecasts, production plans, and inventory data are always up-to-date. This real-time visibility enables operations directors to make informed decisions based on accurate information, enhancing the agility and responsiveness of the organization.
Enhanced Collaboration and Communication: By consolidating data from multiple sources into a single platform, integration between PlanetTogether and enterprise systems promotes collaboration and communication across departments. Sales, operations, and supply chain teams can access relevant information in real-time, collaborate on production schedules, and resolve issues proactively, fostering a culture of transparency and teamwork.
Advanced Analytics and Reporting: With integrated data from PlanetTogether and ERP, SCM, and MES systems, operations directors gain access to advanced analytics and reporting capabilities. They can analyze key performance indicators (KPIs), track production metrics, and identify areas for improvement with greater precision. This data-driven approach empowers operations directors to optimize resource utilization, streamline workflows, and drive continuous improvement initiatives.
Scalability and Flexibility: Integration between PlanetTogether and enterprise systems offers scalability and flexibility to adapt to evolving business needs. Whether scaling production volumes, introducing new product lines, or entering new markets, operations directors can rely on the integrated platform to support their growth aspirations. With robust planning tools and seamless integration, industrial manufacturing facilities can stay ahead of the competition and thrive in today's dynamic marketplace.
Sales and Operations Planning (S&OP) holds the key to unlocking operational excellence in industrial manufacturing. By aligning sales forecasts with production capabilities, S&OP enables operations directors to optimize resource allocation, minimize costs, and maximize customer satisfaction.
When integrated with advanced planning tools like PlanetTogether and leading ERP, SCM, and MES systems, S&OP becomes even more powerful, revolutionizing the way organizations plan, execute, and manage their operations.
As an Operations Director, embracing S&OP and leveraging integrated planning solutions is essential to staying competitive and driving sustainable growth in the ever-changing landscape of industrial manufacturing.
Are you ready to take your manufacturing operations to the next level? Contact us today to learn more about how PlanetTogether can help you achieve your goals and drive success in your industry.