Additive Manufacturing for Medical Device Components
As a plant manager, you're tasked with the responsibility of ensuring that your facility not only meets regulatory standards but also stays ahead of the curve in terms of technology and processes. One avenue that holds immense promise in this regard is additive manufacturing, also known as 3D printing.
In this blog, we'll explore the potential of additive manufacturing specifically for medical device components and how integrating it with advanced planning and enterprise resource planning (ERP) systems like PlanetTogether and others can revolutionize your operations.
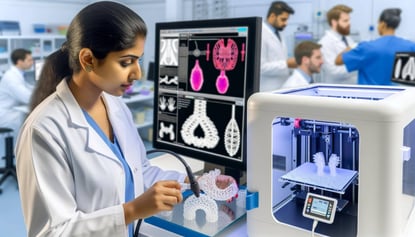
Additive Manufacturing in Medical Device Production
Additive manufacturing has rapidly gained traction across various industries due to its ability to produce complex geometries, reduce material waste, and enable rapid prototyping. In the medical field, these advantages are particularly appealing, given the intricate nature of many devices and the need for customization.
Additive manufacturing allows for the creation of patient-specific implants, prosthetics, surgical instruments, and even tissue scaffolds with unprecedented precision. This level of customization not only improves patient outcomes but also enhances the overall efficiency of the manufacturing process.
Challenges in Integrating Additive Manufacturing
While the potential benefits of additive manufacturing in medical device production are clear, integrating this technology into existing workflows poses some challenges. One of the key hurdles is the seamless integration of additive manufacturing with ERP, supply chain management (SCM), and manufacturing execution systems (MES).
For plant managers, this integration is crucial for ensuring that additive manufacturing processes are synchronized with inventory management, production scheduling, quality control, and regulatory compliance.

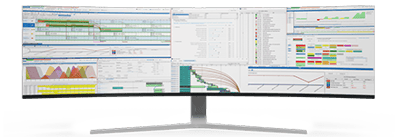
The Role of Advanced Planning Systems
This is where advanced planning systems like PlanetTogether come into play. These software solutions leverage advanced algorithms and data analytics to optimize production schedules, allocate resources efficiently, and minimize lead times.
By integrating additive manufacturing processes with PlanetTogether, plant managers can:
Optimize Production Schedules: Advanced planning systems can analyze real-time data on machine availability, material availability, and order priorities to create optimized production schedules that minimize downtime and maximize throughput.
Manage Inventory Levels: Additive manufacturing reduces the need for maintaining large inventories of spare parts or components. PlanetTogether can help plant managers track inventory levels in real-time and generate replenishment orders automatically, ensuring that production never grinds to a halt due to stockouts.
Ensure Regulatory Compliance: Compliance with regulatory standards such as FDA regulations is non-negotiable in the medical device industry. Advanced planning systems can enforce compliance by incorporating regulatory requirements into production schedules and documentation processes.
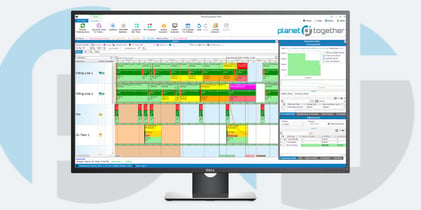
Integration with ERP, SCM, and MES Systems
In addition to advanced planning systems like PlanetTogether, seamless integration with ERP, SCM, and MES systems is essential for realizing the full potential of additive manufacturing in medical device production.
Companies like SAP, Oracle, Microsoft, Kinaxis, Aveva, and others offer comprehensive ERP solutions that streamline various aspects of manufacturing operations, including inventory management, order processing, and financial reporting. Integrating additive manufacturing processes with these ERP systems ensures data consistency across the organization and enables end-to-end visibility into the production process.
Similarly, integration with SCM systems facilitates the efficient management of the entire supply chain, from raw material sourcing to distribution. MES systems play a crucial role in monitoring and controlling the manufacturing process in real-time, ensuring that quality standards are met and production targets are achieved.
Additive manufacturing holds tremendous potential for revolutionizing medical device production. However, realizing this potential requires more than just investing in the latest 3D printing technology. It requires a holistic approach that encompasses advanced planning systems, ERP integration, SCM optimization, and MES control.
As a plant manager, embracing additive manufacturing and integrating it with systems like PlanetTogether and other ERP, SCM, and MES solutions can unlock new levels of efficiency, agility, and innovation in your medical manufacturing facility. By staying ahead of the curve and leveraging cutting-edge technologies, you can not only meet the demands of today's healthcare landscape but also shape the future of medical device production.
Embrace additive manufacturing, integrate with advanced planning systems, and lead your facility towards a future where precision, customization, and efficiency go hand in hand. Are you ready to take your manufacturing operations to the next level? Contact us today to learn more about how PlanetTogether can help you achieve your goals and drive success in your industry.